Overview
The mercury porosimetry analysis technique is based on the intrusion of mercury into a porous structure under stringently controlled pressures. Besides offering speed, accuracy, and a wide measurement range, mercury porosimetry permits you to calculate numerous sample properties such as pore size distributions, total pore volume, total pore surface area, median pore diameter and sample densities (bulk and skeletal).
The AutoPore V Series Mercury Porosimeters can determine a broader pore size distribution more quickly and accurately than other methods. This instrument also features enhanced safety features and offers new data reduction and reporting choices that provide more information about pore geometry and the fluid transport characteristics of your material.
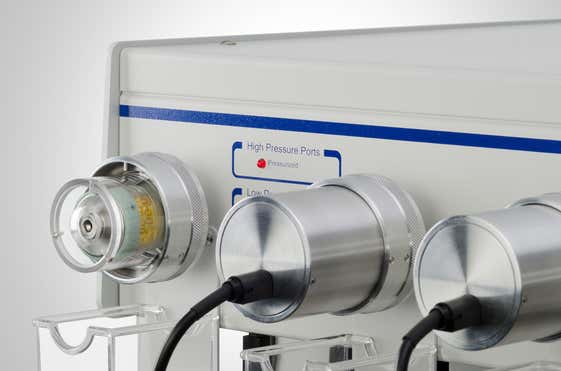
Features
-
Triple fail safe - 2 interlocks on locking caps
Verifies that the capacitance detector is installed on low-pressure port, automatically suspends run, and permits user to check filling of the penetrometer prior to run
-
Mercury collection trays
Safe collection of mercury for disposal in the case of compromised penetrometer seals or operator error resulting in broken penetrometers
-
Improved mercury funnel design
Attached screw cap and funnel-shaped opening eliminates mercury contamination and possible drip-spillage associated with separate detached filling funnel. Attached screw cap prevents loose cap and possible vapor release
-
Mercury vapor detection device
Handheld device to check localized mercury vapor levels that exceed defined safety limits. Portable device allows point checks at the instrument or any location within the lab exposed to mercury
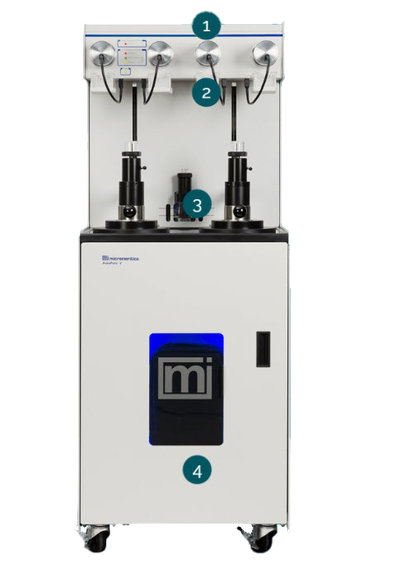
Safety features
- Triple Fail Safe - 1 Penetrometer Safety Cap: In case of operator error, this device prevents the penetrometer or rod being released from port unintentionally
- Triple Fail Safe - 3 System Pressure Vent on Manifold: Works in concert with Cap Interlock to automatically vent system pressure if above ambient pressure and error condition is detected
- Software Control for Fine Powder Samples: Prevents fine powder from accidental aspiration into low-pressure ports during analysis by using intelligent evacuation controlled by sample type
Applications
Porosity and surface area play major roles in the purification, processing, blending, tableting, and packaging of pharmaceutical products as well as a drug’s useful shelf life, its dissolution rate, and bio-availability.
Pore area and porosity affect the curing and bonding of greenware and influence strength, texture, appearance, and density of finished goods.
Knowledge of pore area, total pore volume, and pore size distribution is important for quality control of industrial adsorbents and in the development of separation processes. Porosity and surface area characteristics determine the selectivity of an adsorbent.
The active surface area and pore structure of catalysts influence production rates. Limiting the pore size allows only molecules of desired sizes to enter and exit, creating a selective catalyst that will produce primarily the desired product.
Surface area and porosity of heat shields and insulating materials affect weight and function.
Determine correct composition of catalyst supports and finished products including crystallinity, porosity, and formulation.
Fuel cell electrodes require controlled porosity with high surface area to produce adequate power density.
Porosity is important in groundwater hydrology and petroleum exploration because it relates to the quantity of fluid that a structure can contain as well as how much effort will be required to extract it.
Pore size, pore volume, pore shape, and pore tortuosity are of interest to filter manufacturers. Often, pore shape has a more direct effect upon filtration than pore size because it strongly correlates with filtration performance and fouling.
Diffusion, permeability, and capillary flow play important roles in the degradation processes in concrete, cement, and other construction materials.
The porosity of print media coating is important in offset printing where it affects blistering, ink receptivity, and ink holdout.
Surface area and porosity of heat shields and insulating materials affect weight and function.