A powerful combination: Freeman Technology is a Malvern Panalytical company

Overview
The Freeman FT4 was designed with one purpose in mind: to characterize the rheology of powders, or powder flow properties. This is still the primary function, but the instrument, accessories and methodologies have been continuously developed to the point where the FT4 is now considered a universal powder flow tester.
The FT4 powder tester is unique in many ways. Below are some critical features for assessing industrial value:
- The ability to simulate powder processing conditions, by testing samples in a consolidated, moderately stressed, aerated or fluidized state
- The application of multi-faceted powder characterization to assess dynamic powder flow, bulk, and shear properties to construct the most comprehensive understanding of how a powder behaves
- Unparalleled sensitivity, enabling the differentiation of powders that other testers classify as identical
Freeman Technology, developers of the industry-leading FT4 powder rheometer, became part of the Micromeritics family in 2018. In 2025, Micromeritics and Freeman joined Malvern Panalytical, bringing powder flow expertise into the wider materials characterization portfolio.
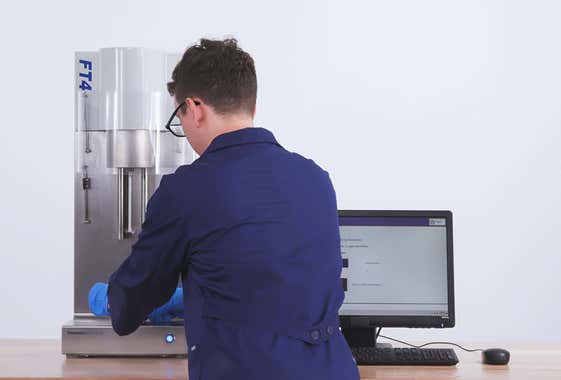
Powder rheometer methodologies
The FT4 is a truly universal powder flow tester offering four categories of methodologies: Bulk, Dynamic Flow, Shear (in accordance with ASTM D7981) and Process.
Applications
The behavior of the powder influences the electrode manufacturing in both wet and dry process. In wet processes, powders with optimal flow and dispersion properties ensure consistent slurries, improving battery performance and manufacturing efficiency.
Additive Manufacturing (AM) relies on precise powder performance to ensure consistency and quality in 3D-printed components. Effective powder spreading and distribution are crucial, as variability can lead to defects like inconsistent density and poor surface finish.
Powder coatings are environmentally friendly as they eliminate solvent use and volatile organic emissions. However, their application is challenging due to the need for smooth powder flow, especially as demand for thinner films requires smaller particles with increased interparticle forces.
Powder processing involves various conditions, from high compaction stresses in hoppers to dynamic fluidization. Understanding how a material behaves across these conditions is crucial for designing and monitoring unit operations and transfer systems.
Toner formulations, often proprietary, are milled into fine powders with sizes <10 μm, making them prone to cohesion and agglomeration. Proper powder flow is crucial to ensure even dispersion and effective adhesion to paper, with additives used to prevent clumping and improve performance.
Cosmetic compacts, made from blends of emollients, pigments, fillers, and binders, must have good powder flow for effective processing. Proper flow ensures consistent quality, ease of application, and cost-effective production at high throughput.
Dry powder pressing is a flexible and cost-effective method for making ceramic components. Identifying the right powder blends and characterization methods is essential for effective process development.
In the food and nutraceutical industries, understanding powder properties and flow behavior is essential for efficient processing. Even small amounts of moisture can drastically affect powders, turning them from free-flowing into clumps or solid masses, which impacts flowability and can lead to reduced efficiency and increased costs.
Powder processing is crucial in pharmaceutical manufacturing, where controlling powder behavior enhances efficiency and quality. Key processes include wet granulation to create uniform, free-flowing granules; die filling; predicting flow performance in screw feeders; and developing dry powder inhaler (DPI) formulations.