Las baterías de iones de litio (Li-ion) se han convertido en el pilar fundamental del almacenamiento de energía moderno, y permiten alimentar todo tipo de dispositivos y maquinaria, desde teléfonos inteligentes hasta vehículos eléctricos. Un componente esencial de estas baterías es el cátodo, en el que se mueven los iones de litio durante la descarga. Por eso, la elección de los materiales del cátodo influye directamente en el rendimiento, la longevidad y la seguridad de la batería. El cátodo deriva de materiales precursores, que normalmente son compuestos de metales de transición. Estos precursores se someten a varios procesos químicos para producir los materiales catódicos activos, que luego desempeñan un papel crucial en las características generales de la batería.
La composición química, la calidad cristalina, el tamaño de partícula y la forma de partícula son los parámetros clave que influyen en la calidad y la eficiencia del proceso de los materiales de precursores catódicos.
Nuestras soluciones
Rango de equipos Mastersizer
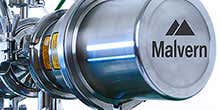
Rango de equipos Insitec
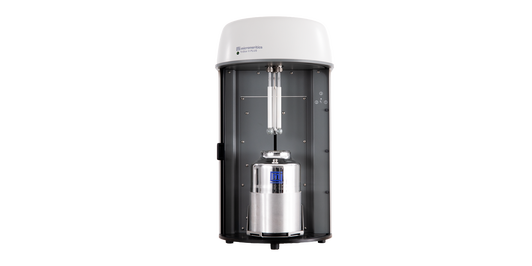
Micromeritics TriStar II Plus
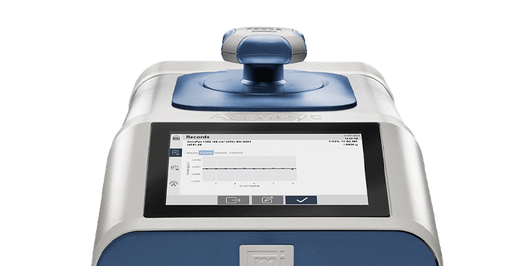
Micromeritics AccuPyc
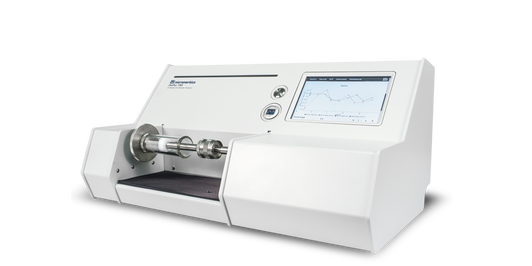
GeoPyc de Micromeritics
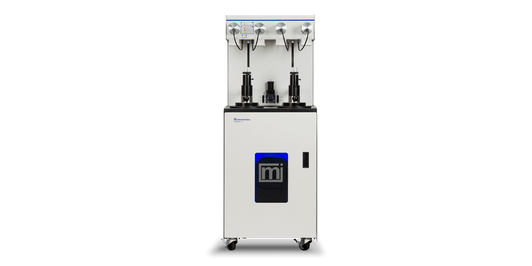
AutoPore V de Micromeritics
Tipos de precursores catódicos
- Precursores de níquel-cobalto-manganeso (NCM) y níquel-cobalto-aluminio (NCA)
El NCM y el NCA se encuentran entre los materiales catódicos más populares de la industria, especialmente para vehículos eléctricos. Los precursores de estos materiales son hidróxidos mixtos, denotados como NixCoyMn(1-x-y)(OH)2 para NCM y NixCoyAl(1-x-y)(OH)2 para NCA. - Precursor de óxido de cobalto de litio (LCO)
El óxido de cobalto de litio (LiCoO2) se usa ampliamente en dispositivos electrónicos portátiles. El precursor, óxido de cobalto (Co3O4), se procesa con carbonato de litio o hidróxido de litio para producir el material del cátodo final. - Precursor de fosfato de hierro y litio
Los cátodos de fosfato de hierro y litio (LiFePO4), empleados en baterías de vehículos eléctricos, derivan de precursores de fosfato de hierro (FePO4). - Precursor de manganeso y litio (LMO)
El óxido de manganeso (Mn3O4) actúa como el precursor del óxido de manganeso litio (LiMn2O4), un material conocido por su alta capacidad y buena estabilidad térmica, y que a menudo se utiliza en vehículos híbridos y herramientas eléctricas. - Precursores ricos en níquel
Con la necesidad de mayores densidades de energía en las baterías, los precursores ricos en níquel están ganando preponderancia. Estos precursores, a menudo representados por Ni(OH)2 con cantidades variables de dopantes, se utilizan para producir materiales catódicos con alto contenido de níquel.
Síntesis y procesamiento de precursores
El método más común para sintetizar los precursores catódicos es la coprecipitación, en la cual las soluciones acuosas de las sales metálicas se mezclan para formar precursores líquidos. Se agrega un agente precipitante, como hidróxido de sodio (NaOH) o hidróxido de amonio (NH4OH), a la solución, lo que provoca que los metales se precipiten como hidróxidos.
La coprecipitación es un proceso lento: empieza por la nucleación, seguida del crecimiento de las partículas primarias y, finalmente, la aglomeración de las partículas secundarias más grandes. Todo el proceso puede tardar entre 20 y 40 horas, en función de su eficacia.
La temperatura, el pH, la concentración y la velocidad de agitación de la solución se controlan cuidadosamente para garantizar un tamaño y una composición uniformes del precipitado. Por lo general, el producto precipitado es un hidróxido de metal o carbonato mezclado, como NixCoyMn(1-x-y)(OH)2 para los precursores de NCM. A continuación, este precursor se mezcla con LiOH y se calcina a 900 °C para obtener el material catódico final. El proceso se muestra esquemáticamente a continuación.
Muchos parámetros, como la composición de la lechada, el pH, la temperatura y la velocidad de agitación, influyen en la eficacia de la coprecipitación. La optimización de estos parámetros desempeña una función fundamental en la calidad y el rendimiento de los materiales de precursores catódicos para baterías. Para supervisarlos y controlarlos en tiempo real a fin de mejorar la eficiencia del proceso de coprecipitación, ofrecemos una amplia gama de soluciones analíticas. Además, nuestras soluciones también pueden ayudarlo a garantizar que su material precursor tenga las propiedades deseadas para su posterior transformación en el material catódico activo.
¿Cómo puedo optimizar mis materiales de precursor de cátodo?
La calidad y el rendimiento del precursor catódico pueden optimizarse midiendo y controlando los siguientes parámetros:
- Tamaño de partícula
- Forma de partícula
- Composición química e impurezas
- Análisis de fase cristalina
- Potencial zeta
Encontrará más información sobre cada parámetro a continuación.
Tamaño de partícula
Las partículas precursoras forman un núcleo, crecen y, a continuación, se aglomeran para formar partículas secundarias de mayor tamaño. Para garantizar la máxima eficiencia de producción, estas partículas deben crecer por sobre su tamaño objetivo en el menor tiempo posible. La medición del tamaño de las partículas en función del tiempo es, por tanto, una forma importante de ajustar con precisión los parámetros del proceso en el reactor de lechada.
Rango de equipos Mastersizer
La forma más inteligente de medir el tamaño de las partículas
La difracción láser es una de las mejores maneras de medir con exactitud la distribución del tamaño de partícula para el proceso y el control de calidad. Con la confianza de los fabricantes de celdas y materiales para baterías de todo el mundo, Mastersizer 3000 se ha convertido en el estándar de facto para el análisis del tamaño de partículas.
La gama Mastersizer de analizadores de tamaño de partículas por difracción láser es un referente en la obtención de distribuciones de tamaño de partículas rápidas y precisas para dispersiones húmedas y secas. Y ha mejorado aún más con la introducción del NUEVO Mastersizer 3000+ con funcionalidades avanzadas como Size Sure y Data Quality Guidance.
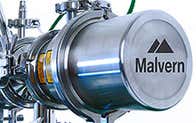
Rango de equipos Insitec
Sólido, confiable, medición de tamaño de partículas en tiempo real
Nuestro analizador de tamaño de partículas Insitec automatizado en línea es ideal para realizar estas mediciones en un entorno de producción, ya que proporciona análisis en tiempo real cada pocos segundos.
Con un bucle de retroalimentación, esta información se puede utilizar para ajustar parámetros como el pH, la temperatura o la velocidad de agitación.
Es más, también puede garantizar la sinergia con flujos de procesos de fabricación inteligentes. Esto ofrece grandes beneficios: normalmente, una planta de fabricación de cátodos que produce 1000 kg de material catódico al día puede ahorrar hasta 200 000 USD al año mediante el análisis del tamaño de partícula de la lechada precursora con el Insitec.
Forma de partícula
La forma de las partículas desempeña un papel importante en la formación de partículas secundarias estables y puede influir significativamente en el rendimiento del precursor (densidad compactada), así como en la calidad del material catódico final. Por ejemplo, es más probable que las partículas alargadas se rompan y se vuelvan a disolver en una lechada agitada a alta velocidad.
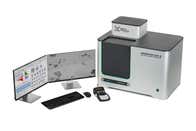
Morphologi 4
Análisis rápido y automatizado del tamaño y la forma de las partículas
Para que los fabricantes puedan analizar y optimizar la forma de las partículas, nuestra herramienta de adquisición de imágenes ópticas Morphologi 4 puede utilizarse para medir parámetros como la circularidad, la relación elongación/aspecto, el diámetro circular equivalente (CE) y la transparencia, con su análisis de imágenes totalmente automatizado.
Composición química e impurezas
Para lograr una composición química óptima en los materiales catódicos finales, primero debe controlarse a nivel de precursores. La fluorescencia de rayos X (XRF, del inglés “X-Ray Fluorescence”), que puede analizar la composición química y las impurezas desde unas pocas ppm hasta el 100 %, es la mejor técnica para analizar la composición química.
La XRF permite medir la composición elemental de forma más sencilla y precisa que la espectrometría de masas con plasma acoplado inductivamente (ICP, del inglés “Inductively Coupled Plasma”), ya que no requiere dilución de la muestra ni digestión ácida. Muchas empresas líderes en baterías utilizan nuestros espectrómetros de sobremesa Epsilon 4 EDXRF o Zetium WDXRF para analizar la composición de sus materiales precursores y catódicos.
Como complemento, este es nuestro nuevo sistema de EDXRF de alta gama Revontium. En combinación con nuestro conjunto de estándares de referencia para baterías, los sistemas de fusión Forj/Egon 2 y nuestra experiencia, ofrecemos una solución completa que puede igualar o superar la precisión y exactitud del análisis de ICP.
Las soluciones de análisis de composición elemental en línea incluyen Epsilon Xflow para precursores líquidos de baterías y Epsilon Xline para analizar el revestimiento del electrodo.
Análisis de fase cristalina de materiales para precursores catódicos
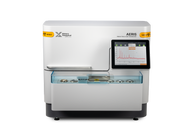
Aeris
El futuro es compacto
La fase cristalina se refiere a la estructura de los materiales a escala atómica, que corresponde a aquella en la que se produce o se dificulta el transporte iónico o electrónico. La composición de la fase cristalina del precursor puede proporcionar una indicación temprana de la calidad del material del cátodo final.
Para analizar con precisión la composición de la fase cristalina de los materiales de precursores catódicos, los fabricantes pueden utilizar nuestro difractómetro de rayos X compacto Aeris, un instrumento fácil de usar con una calidad de datos excelente.
Análisis del potencial zeta
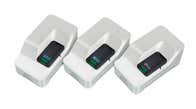
Gama Zetasizer Advance
Dispersión de luz para cada aplicación
La precipitación de partículas a partir de la solución precursora catódica se basa en la interacción de partículas primarias (de 50 a 100 nm) para formar partículas secundarias de mayor tamaño (de 10 a 20 µm). El potencial zeta se puede utilizar para analizar y ajustar los valores de pH y temperatura con el fin de optimizar estas interacciones.
Nuestro Zetasizer mide con precisión el potencial zeta y también puede complementar su I+D en la síntesis de precursores.
Otras lecturas
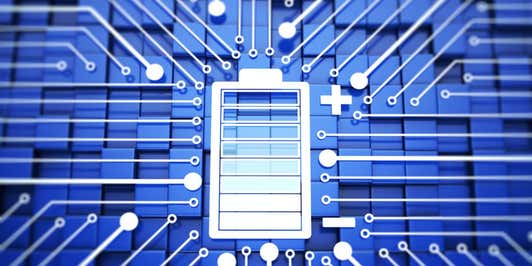
What XRD configuration shall one use to analyze battery cathode materials?
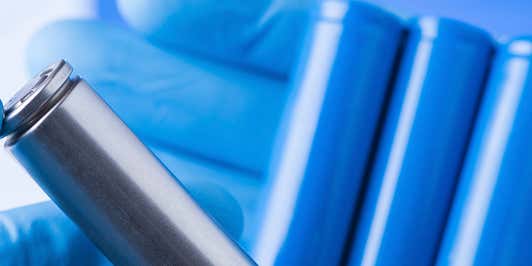
Analytical toolkit for the optimization of battery electrode materials
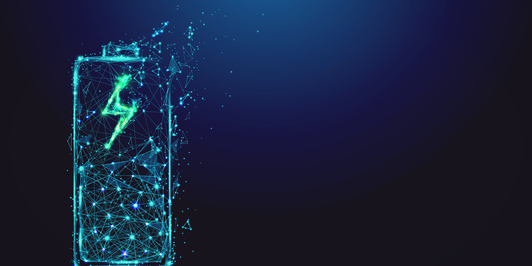
Battery manufacturing: Reliable, adaptable particle sizing using the Mastersizer 3000+
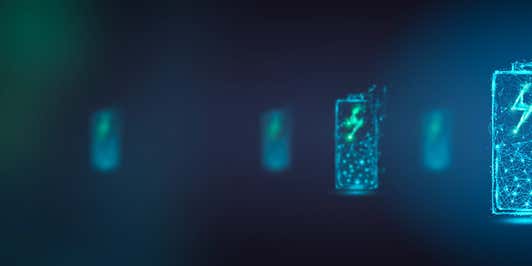
XRF Analysis of Lithium Iron Phosphate Cathodes
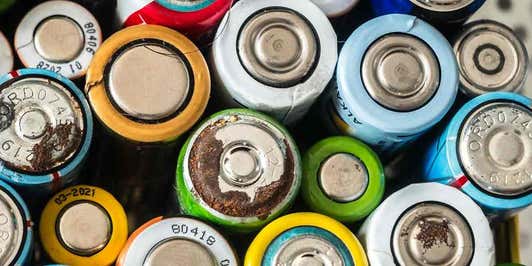
Reciclaje de baterías de iones de litio
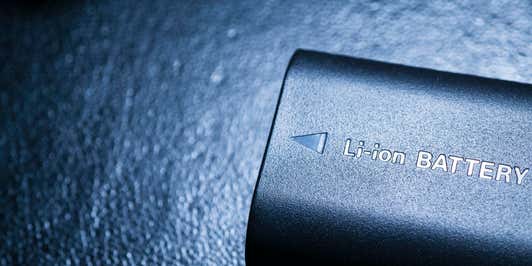
In operando XRD
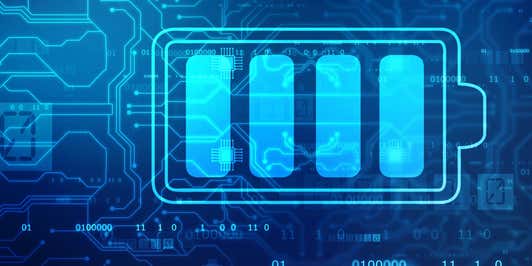
Baterías y supercondensadores
Nuestras soluciones
Rango de equipos Mastersizer
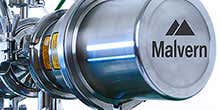