For additive manufacturers producing high volumes of 3D components, binder jetting is often used, thanks to its high speed and output. Binder jetting processes can be considered a subset of powder bed technology, since they operate in a very similar way. However, in binder jetting, a liquid binding agent is used to join the metal, ceramic, or polymer powder particles rather than melting or fusing them together with a laser or electron beam. This results in the formation of a ‘green part’ that is removed from the printer with solidification via a secondary de-binding or sintering step.
To ensure that this ‘green part’ and the final components are of consistent quality, the powder’s material characteristics, such as particle size and particle shape, chemistry, and microstructural characteristics, should be optimized. Malvern Panalytical offers a range of material characterization solutions to support additive manufacturers with this.
Please download our brochure to find out more.
Material particle size distribution analysis
Particle size distribution is critically important for binder jetting, since it affects powder bed packing and flowability – which, in turn, affects build quality and final component properties.
To measure the particle size distribution of metal, ceramic, and polymer powders for binder jetting, laser diffraction is an established technique used by powder producers, component manufacturers, and machine manufacturers worldwide to qualify and optimize powder properties. Malvern Panalytical provides instruments to support these manufacturers with laser diffraction. Using our Mastersizer in a laboratory setting, or using Insitec online, laser diffraction can provide a complete high-resolution particle size distribution.
Featured products
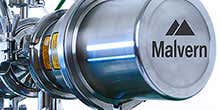
Rango de equipos Insitec
Binder jetting component particle shape optimization
Both particle size and shape influence powder bed density and powder flowability. Since these, in turn, affect final component properties, particle shape is another property that it’s important to optimize in binder jetting. Smooth, regular-shaped particles are preferable because they can flow and pack more easily than those with a rough surface and/or irregular shape.
To enable additive manufacturers to achieve this regular shape, the Morphologi 4 automated imaging system can be used to classify and quantify the size and shape of metal, ceramic, and polymer powders. It does this by combining particle size measurements, such as length and width, with assessments of particle shape features, such as circularity and convexity (roughness).
Metal alloy powder elemental analysis
Analyzing the elemental composition of metal alloy powders is particularly important in binder jetting, since small variations in the concentration of alloying elements can affect its chemical and physical properties – including strength, hardness, fatigue life, and chemical resistance. To detect these variations, contaminants, or inclusions in metal alloys and ceramics, X-ray fluorescence (XRF) is an effective technique to determine the elemental composition, offering significant time and cost savings compared with alternative techniques. Malvern Panalytical’s XRF systems, such as our Zetium and Epsilon, can support additive manufacturers with this. For ceramics, X-ray diffractometers such as our Aeris can also be used to determine chemical composition.
When it comes to evaluating the chemical properties of polymeric materials, the Morphologi 4-ID, which combines automated imaging with Raman spectroscopy, can be used to obtain particle-specific chemical information. Our Labspec near-infrared spectrometer can also be used for the chemical analysis of polymers.
Featured products
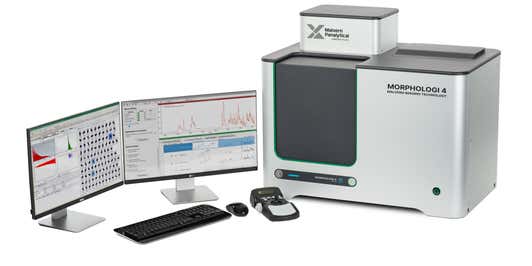
Morphologi 4-ID
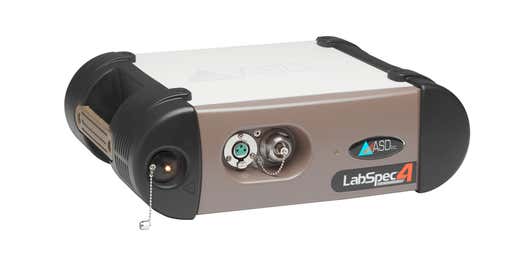
Gama de equipos ASD LabSpec®
Powder microstructure characterization
Analyzing powder’s microstructural characteristics – such as phase composition, residual stress, grain size, and grain distribution (texture) – is critically important for metal additive manufacturing, since they can affect the chemical and mechanical properties of the final manufactured component.
X-ray diffraction (XRD) systems are an effective way to analyze these microstructural characteristics and optimize the final component’s properties. To support additive manufacturers with this, Malvern Panalytical offers a range of material analysis solutions. For instance, benchtop XRD systems such as our Aeris are an effective solution for conducting phase analysis of metals. For additional information on texture, grain size, and residual stress under a wide range of conditions, multi-purpose diffractometers like the Empyrean can be used. What’s more, XRD is also widely used to study the structure and crystallinity of polymers and ceramics.
Our solutions
Rango de equipos Mastersizer
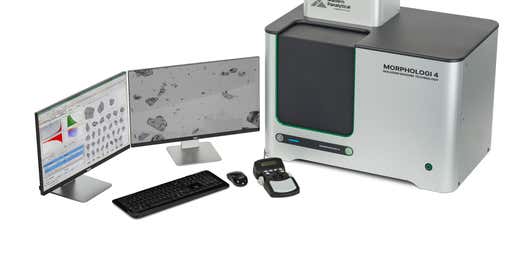
Morphologi 4
Featured content
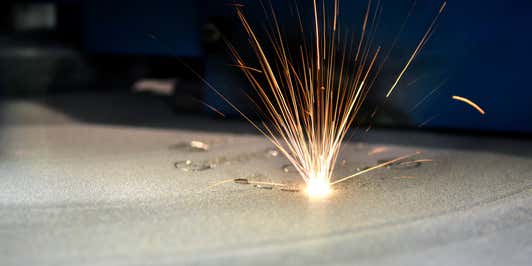
Exploring the role and measurement of particle size and shape in metal additive manufacturing
Practical small spot mapping. Analysis of a ceramic inclusion using SumXcore technology
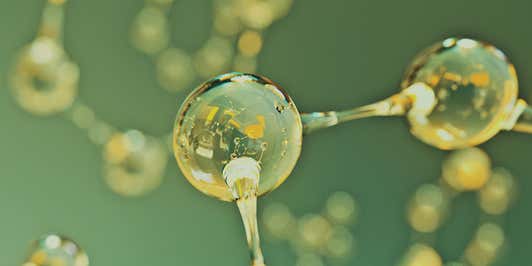