To improve the mechanical properties and workability of additive manufacturing materials, many manufacturers use isostatic pressing. This is a component-forming process where pressure is applied uniformly (using gas or liquid) to a hermetically sealed container filled with compacted metal powder. Isostatic pressing can be performed at elevated temperatures, known as hot isostatic pressing (HIP), or at ambient temperatures, known as cold isostatic pressing (CIP). Hot isostatic pressing can be used to manufacture metal components directly, or to densify parts from other powder metallurgy processes.
Isostatic pressing has several benefits over the commonly used press and sinter method, including equal compaction in all directions and a more uniform final component density. Nevertheless, as with other powder metallurgy processes, manufacturers must carefully characterize the metal powder’s properties for isostatic pressing to be successful. Malvern Panalytical offers several solutions to support this.
Please download our brochure to find out more.
Why is material characterization important?
Like other powder metallurgy processes, the properties of the metal powder used in isostatic pressing will affect the final sintered component’s properties. For this reason, these properties should be carefully characterized to ensure optimum final component properties.
For example, spherical powders with a relatively wide but consistent particle size distribution are preferred for HIP because they produce higher fill densities. For CIP, some particle irregularity may help increase cold-welding, ideally without compromising powder flow and packing.
Phase composition and grain size are also important characteristics to control, because they can affect powder hardness and melt properties. These, in turn, affect not only pressing efficiency and sintering behavior but also the mechanical properties of the pressed part. Finally, the powder used must also comply with the alloy composition of the material specified.
Featured content
Using X-rays to see inside your powdered metal materials and processes
A tale of two processes – sieve analysis and laser diffraction
Live demo at your desk: latest high performing XRD Benchtop
How can Malvern Panalytical’s solutions help?
To enable manufacturers to control these characteristics, Malvern Panalytical offers several characterization solutions for isostatic pressing. They can be used to:
- Predict and control packing density and minimize void formation in the sintered part
- Specify and control metal powder quality – including particle size, shape, and elemental composition
- Optimize powder flow in the mold and maintain process efficiency
- Ensure pressed parts have the appropriate composition and grain structure, and are free from residual stresses
Our solutions
Mastersizer range
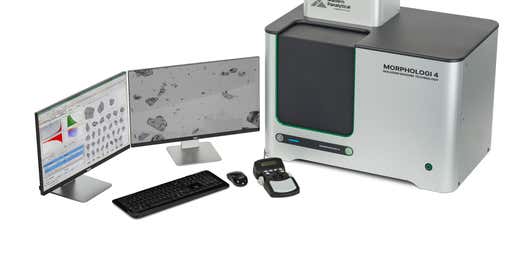