Powder injection molding (PIM) and metal injection molding (MIM) are powder metallurgy processes in which fine metal or ceramic powders are mixed with a binder material to create a feedstock. The feedstock is then injection molded to form a ‘green part’. After molding, the part undergoes a de-binding and final sintering step to fuse the powders into a dense part.
To produce feedstock, green parts, and ultimately final components of consistent quality, manufacturers carrying out PIM and MIM need to carefully characterize the properties of their metal or ceramic powder particles. To meet this need, Malvern Panalytical offers several material characterization solutions suitable for powder injection molding and metal injection molding applications.
Please download our brochure to find out more.
Why is material characterization important?
In PIM and MIM applications, the feedstock’s rheological properties are very important because they influence the homogeneity of the molten feedstock, how well it flows through the die into the mold cavity, and the mechanical properties of the green part on cooling. These rheological properties are influenced by several factors, including the binder’s molecular weight and molecular structure, solid loading, particle size and particle shape, temperature, and flow rate. Most metals and ceramics can be used in PIM if they have the correct powder properties, including particle size and shape.
So, to produce high-quality feedstock, green parts, and ultimately final components – and to have a wide choice of materials – manufacturers must carefully characterize these properties. In particular, high packing densities are required, so spherical particles with the correct size distribution are preferable, as are smaller particles (< 38μm) that sinter more readily. Slight particle irregularity can be beneficial to give mechanical strength to green and brown parts.
Featured content
Using X-rays to see inside your powdered metal materials and processes
Zetium - NiFeCo-FP - analysis of steels, high-temperature alloys and super alloys
Comparing metal powders from different atomization processes using automated image analysis
How can Malvern Panalytical’s solutions help?
Malvern Panalytical’s material characterization solutions for powder injection molding can be used to:
- Optimize particle loading to minimize part shrinkage and void formation
- Ensure appropriate feedstock rheology during molding and dimensional stability post-extrusion
- Optimize binder properties, including molecular weight and structure, for flow behavior and de-binding performance
- Ensure consistent metal powder supplies with the correct particle size, elemental composition, and microstructure
Our solutions
Mastersizer range
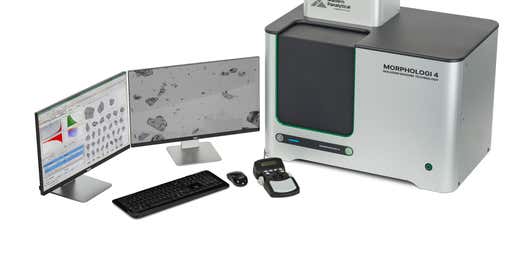