既存または新規の鉄鉱石鉱床の鉱石グレードを下げる場合、最適で収益性の高い選鉱を行うために、鉄鉱石を効率的に選別して混合する予測ソリューションが必要です。鉄鉱石生産者にとっては、洗浄可能な成分などの冶金パラメータに基づいた、元素および鉱物組成、およびアップグレード可能性の予測モデルが重要な役割を果たしています。
当社のソリューションは、コンベアベルトの直接分析から、鉄鉱石、鉄焼結体、還元鉄、銑鉄、鉄鉱石ペレットのラボ分析および完全な自動品質管理に至るまで、製鉄プロセス全体を監視します。鉄鉱石の生産プロセス全体を通して、当社は、探査地質学者、鉱山計画者、プロセスエンジニア、幾何学冶金学者、品質管理者向けに、カスタマイズされた分析ソリューションを提供しています。
鉄鉱石の採掘
鉄鉱石を採掘する前に、鉱床を評価して、最適な計画、掘削予算の使用、鉄鉱石選鉱用機器の選択のために、鉱体内のグレード分布に関する知識を得る必要があります。
当社は、鉱物(NIR)および元素(XRF)分析により、現場で直接グレードを定義できる分析ソリューションを提供しています。あらゆる鉱山の特定の要件に合わせて調整されたラボソリューションは、ベンチトップ型、スタンドアロン型、または完全に自動化された採掘ラボソリューションのいずれであっても、正確な情報を提供します。
鉄鉱石サンプル調製の専門知識、特に融接機を使用した高品質のガラスディスクの製造に関する当社の専門知識は、国際基準に準拠した正確な元素分析の基礎となります。
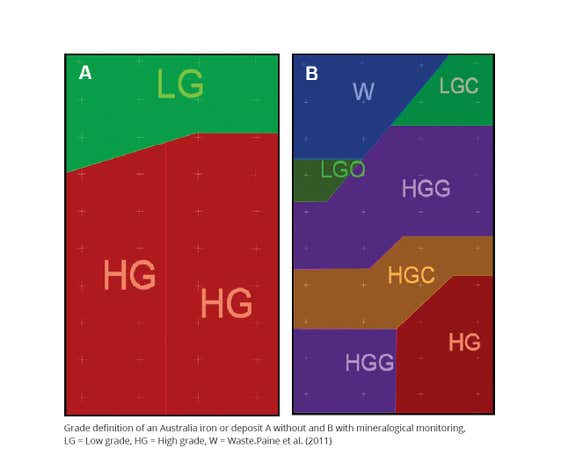
鉄鉱石グレードの定義
当社の専門知識により、鉄鉱石採掘業者は鉱石グレードを定義して、正確な鉱山計画を確かなものにし、鉄鉱石のアップグレード可能性を予測することで、誤って分類されることによるグレードブロックあたり100万米ドル以上を節約できます。
当社のオンライン分析(元素分析および鉱物分析)ソリューションは、鉱山内で直接使用するため、鉄鉱石組成の変化に対する鉱石の選別と迅速な対応が可能になり、下流工程に最適な混合物が生成されます。
これにより、採掘作業の経費を毎月数百万米ドル節約できます。鉄鉱石の選鉱は、鉱石1トン当たりのコストを大幅に増加させるからです。
鉱山コンベアベルト(NIR)の水分含有量を制御するとともに、出荷前に鉄鉱石の組成を正確に監視することで、一定の鉱石品質が保証され、違約金を回避できます。
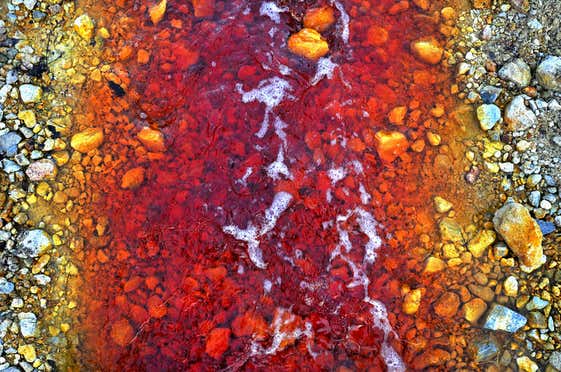
廃棄物管理
廃棄物管理は、持続可能で危険のない採掘と鉄鉱石の選鉱のために非常に重要です。元素分析、粒子径および形状の特性評価、ゼータ電位の監視、粘土鉱物の特性評価のための専用分析ソリューションにより、持続可能な鉱山運営が実現します。
製鉄
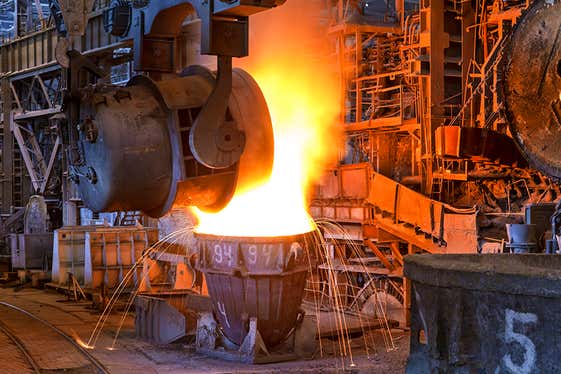
鉄鉱石を効率的に処理して高品質な鉄鋼生産を実現するためには、下流工程のすべての段階で頻繁に鉱石グレードを監視することが必須です。製鉄法に関係なく、競争力を維持し、環境に優しい生産を実現するためには、焼結、ペレット化、鉄鉱石の直接還元(DRI)中に燃料とエネルギーを最適に使用する必要があります。
当社のオンラインレーザー回折ソリューションを使用したペレットフィードのリアルタイム粒子径監視は、高品質の鉄鉱石ペレットを実現するための基礎であり、ペレット化条件の予測に役立ちます。
ペレットまたは焼結製造用の原料混合物の元素組成は、当社の中性子分析装置を使用して採掘コンベアベルト上でオンラインで監視することも、高スループット産業向けに当社の蛍光X線分析装置を使用してラボで監視することもできます。
Analysis of iron sinter by X-ray diffraction reduces CO2 emissions
鉱物組成
鉄ペレット、焼結体、または還元鉄の鉱物組成を知ることで、高炉内の特性と挙動を予測することができます。当社の産業用X線回折装置と統計的手法を組み合わせることで、物理的パラメータを数分以内で監視できます。
- 鉄ペレットの圧縮強度、
- 低温劣化または鉄焼結体のFe2+含有量
- 還元鉄の金属化の程度または炭素含有量
これにより、危険な湿式化学物質の使用が回避され、安全なサンプル処理と時間を必要とする物理的テストが確かなものになります。