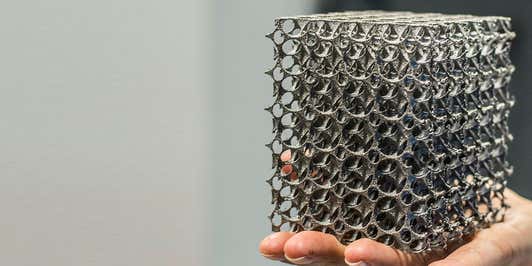
Metal powders or powdered metals are used in a wide range of applications such as coatings, pigments, pyrotechnics, and batteries. The largest, fastest-growing applications for metal powders are the powder metallurgy and additive manufacturing segments, which are near net shape manufacturing technologies for producing parts close to their final size and shape with minimal finishing.
Traditional powder metallurgy processes such as press and sinter have been used to produce metallic components since the 1920s, while processes such as hot isostatic pressing (HIP) and metal injection molding (MIM) have been employed since the 1960s and 70s, respectively. Additive manufacturing is a relatively new technology that enables local fusing of metal powders using a laser, electron beam, or by post-sintering adhesive-bonded powders.
The main routes for manufacturing metal powders are:
- Comminution of solid metal
- Precipitation of a salt from solution
- Thermal decomposition of metal carbonyl (carbonyl process)
- Solid state reduction of metal oxide
- Electrodeposition
- Atomization of molten metal
The choice of powder manufacturing route depends on the metal or alloy being produced, the end-use application, and the specific powder properties required for that process. For example, gas-atomized metal powders are used in many powder metallurgy applications, but certain size fractions are often needed to give the required properties.
Please download our brochure to find out more.
Why is material characterization important?
Consistently producing metal components or products with the correct properties requires input materials with known and reliable characteristics. For metal powders, these can include chemistry, morphology, and microstructural characteristics that must be measured using the appropriate metal analysis techniques.
Which characteristics of metal powders are important?
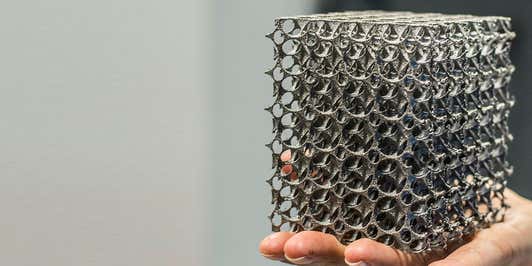
Particle size and shape are key properties for most metal powder processes since they impact powder flow, powder packing, porosity, reactivity, and even health and safety. These properties need to be optimized for the particular end process, whether it is spraying, spreading, pressing, or sintering. Chemistry is also paramount, especially for powder metallurgy and additive manufacturing, in which powder needs to comply with the alloy composition of the material specified and grade must be carefully selected to control the interstitial elements present.
Crystallographic structure is also important as this can affect the mechanical and chemical properties of metal powders and fabricated components alike. It is often necessary to engineer powders to have a certain phase composition and grain size and texture for the application of interest.
Rheological properties also become important for processes such as metal injection molding, in which the feedstock material is a dispersion of metal powder in a polymer/wax matrix, or printing inks containing dispersed metal pigments. These properties are influenced by particle characteristics, including particle size, shape, and concentration.
What metal powder analysis solutions does Malvern Panalytical offer?
Our key solutions for particle characterization are the Mastersizer and Morphologi 4, which are highly automated benchtop instruments. The Mastersizer 3000 uses laser diffraction to measure particle size distribution, and this technique can also be employed on-line using Insitec. Morphologi 4 is an automated imaging system that uses a digital camera to capture high-quality 2D images of dispersed particles and provides particle-specific size and shape information. For metal nanoparticles and dispersions, our Zetasizer range can be a more appropriate solution. This employs dynamic light scattering and electrophoretic light scattering to measure particle size and zeta potential, respectively.
For elemental analysis, we employ X-ray fluorescence (XRF), which is available as floor-standing (Zetium) and benchtop (Epsilon) variants, depending on application requirements. We also provide several sample preparation solutions for XRF, ICP, and AA through our Claisse portfolio. For structural and crystallographic studies, X-ray diffraction (XRD) is our principal solution and also available as a floor-standing (Empyrean) and benchtop (Aeris) systems.
Featured content
Optimizing metal powders for additive manufacturing
Determining the particle size distribution of metal powders using wet and dry dispersion on the Mastersizer 3000
Characterizing the particle size and shape of metal powders for Additive Layer Manufacturing
Zetium - NiFeCo-FP - analysis of steels, high-temperature alloys and super alloys
Additive manufacturing of Inconel 718: characterizing parts and powders
Optimizing metal powders for Isostatic Pressing
Our solutions
Mastersizer range
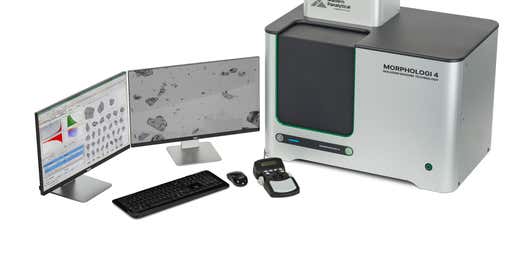
Morphologi 4
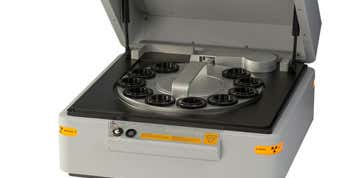