Non-ferrous metals, which include aluminum, copper, lead, nickel, tin, titanium, zinc, and their alloys, are essential to numerous industrial applications. As a result, strict requirements for major, minor, and trace elements at concentrations from sub-ppm to percentage level apply to these metals.
Highly accurate chemical analysis techniques are therefore a must-have in non-ferrous metal production. Proven techniques include X-ray fluorescence and pulsed fast thermal neutron activation (PFTNA) for elemental analysis, X-ray diffraction for phase characterization, and laser diffraction for particle size and size distribution analysis. These techniques provide both the accuracy to meet quality standards and the high throughput necessary to streamline production.
Types of non-ferrous metals and alloys
- Copper
Known for its excellent electrical conductivity, copper is widely used in wiring, electronics, and plumbing systems.
- Nickel
Nickel offers high corrosion resistance and strength, making it ideal for alloys used in harsh environments.
- Aluminum
Lightweight yet strong, aluminum is valued in aerospace, construction, and packaging due to its versatility and corrosion resistance.
- Zinc
Commonly used for galvanizing steel, zinc provides a protective coating that resists rust and extends the life of metal components.
Types of non-ferrous metals
CopperKnown for its excellent electrical conductivity, copper is widely used in wiring, electronics, and plumbing systems. | NickelNickel offers high corrosion resistance and strength, making it ideal for alloys used in harsh environments. | AluminumLightweight yet strong, aluminum is valued in aerospace, construction, and packaging due to its versatility and corrosion resistance. Learn more. | ZincCommonly used for galvanizing steel, zinc provides a protective coating that resists rust and extends the life of metal components. |
How do you identify non-ferrous metals?
Identifying non-ferrous metals accurately is essential for quality control, recycling, and industrial applications.
Several advanced analytical technologies are used to determine their composition and structure:
X-Ray fluorescence (XRF)
XRF is a fast, non-destructive technique ideal for determining the elemental composition of non-ferrous metals.
When exposed to X-rays, each element emits a unique fluorescent signal. This allows the rapid identification and quantification of elements like copper, nickel, aluminum, and zinc – making it especially useful for alloy verification and scrap metal sorting.
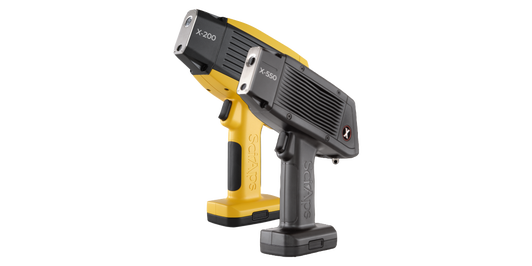
SciAps X-Series
X-Ray diffraction (XRD)
XRD is used to identify the crystalline structure of metals and their alloys. It’s particularly useful for detecting different phases within a sample, such as the presence of specific compounds or differentiating between similar alloys with varying crystal structures.
This makes XRD ideal for quality control in metal production and failure analysis.
Laser diffraction
While not used to identify elements or phases directly, laser diffraction is valuable for measuring the particle size and size distribution of metal powders.
This is crucial in additive manufacturing, metallurgy, and metal processing, where the performance of non-ferrous metal powders – like those made from aluminum or copper – depends heavily on particle size and uniform size distribution.
Pulsed fast thermal neutron activation (PFTNA)
PFTNA enables real-time, multi-elemental analysis of bulk materials on conveyor belts.
By bombarding material with pulsed neutrons and analyzing emitted gamma rays, PFTNA can quantify both heavy and light elements, even in heterogeneous or moist samples. This makes it ideal for upstream process control, especially in the mining and refining of non-ferrous metals.
Cross-belt PFTNA analyzers help reduce variability in feedstock, optimize blending, and maintain consistent input quality.
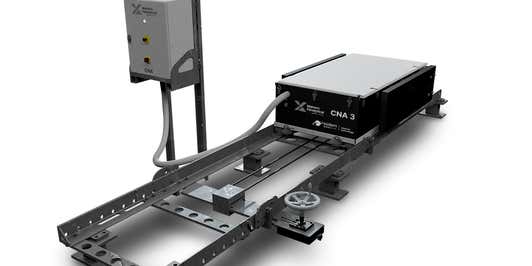
CNA³ elemental cross-belt analyzer
Are non-ferrous metals sustainable?
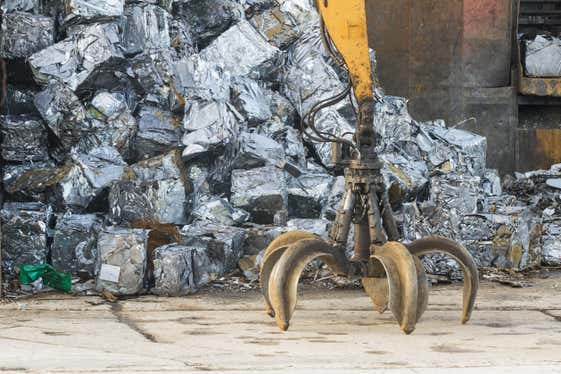
Non-ferrous metals provide several sustainability advantages, chiefly through their recyclability and energy-efficient properties. They can be recycled indefinitely, reducing reliance on primary extraction and thereby minimizing the carbon emissions associated with metal production. Their low weight also lowers the energy costs of transportation, further contributing to the reduction of greenhouse gas emissions.
Non-ferrous metals serve as essential components in many renewable energy generation and storage technologies. Copper and aluminum are fundamental to the construction of solar panels, wind turbines, and electrical grids, enabling the efficient transmission and distribution of renewable power. Furthermore, metals like lithium, cobalt, and nickel play a critical role in rechargeable batteries, facilitating the storage of renewable energy for use in electric vehicles, energy storage systems, and grid stabilization.
The sustainability of non-ferrous metals hinges on responsible sourcing, recycling practices, and environmental management. By enabling more efficient and reliable quality control, analytical technologies like XRF, XRD, laser diffraction, and PFTNA can play a key role in the sustainability of the non-ferrous metals industry.
What is the difference between ferrous and non-ferrous metals?
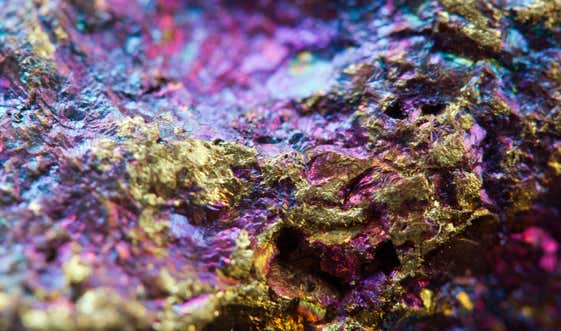
Ferrous and non-ferrous metals are two broad categories that differentiate metals based on their iron content. The primary distinction between them lies in whether or not they contain iron, which significantly impacts their properties and applications.
Ferrous metals contain iron, making them prone to rust and corrosion when exposed to moisture and oxygen. Examples include steel and cast iron, renowned for their strength and durability in construction and manufacturing.
On the other hand, non-ferrous metals like aluminum and copper, and alloys like brass do not contain iron, offering advantages such as corrosion resistance, lightweight properties, and high conductivity.
In terms of analysis, ferrous metals are often tested using methods such as X-ray fluorescence (XRF) or spark testing to determine their composition and quality, given the importance of iron content.