Lithium-ion batteries use various metals, such as lithium, nickel, manganese, cobalt, and aluminum. Mining these metals can be environmentally damaging. Some of them, like lithium and cobalt, are available only in limited quantities – so widespread usage of lithium-ion batteries is likely to drive up their prices. What’s more, they are often toxic and can contaminate soil and groundwater if they end up in landfills at the end of their life.
Lithium-ion battery recycling can keep this toxic waste out of landfills, in addition to providing more raw materials to build a sustainable battery value chain. But to be recycled, the batteries’ chemistry must first be evaluated. To help you unlock commercially viable recycling options, our X-ray-based solutions can help provide these insights into the chemistry of your used batteries.
Our solutions
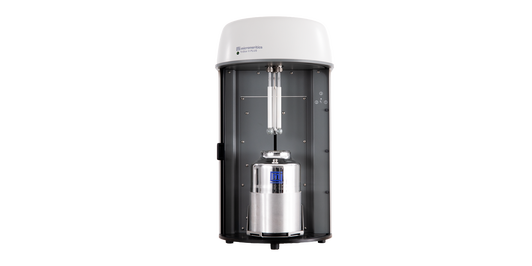
Micromeritics TriStar II Plus
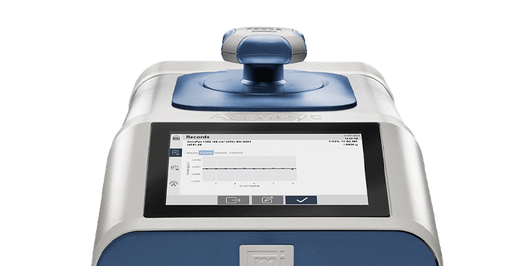
Micromeritics AccuPyc
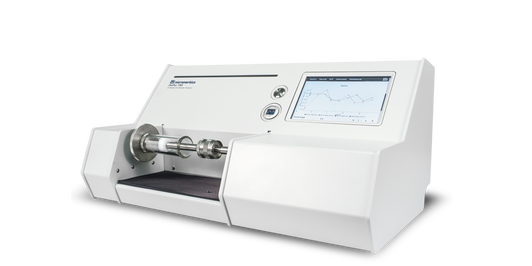
Micromeritics GeoPyc
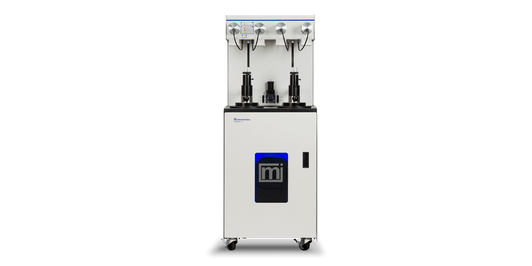
Micromeritics AutoPore V
How lithium-ion batteries are recycled
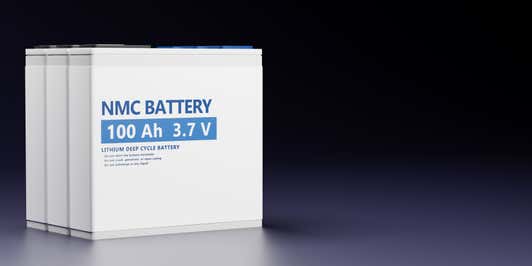
Elemental composition analysis of Nickel-Manganese-Cobalt cathodes and their precursor materials using Zetium WDXRF
The recycling of lithium-ion (Li-ion) batteries involves collecting and sorting the used batteries, discharging them to ensure safety, and then dismantling them to separate the components. The cells are crushed and shredded, with the resulting material sieved and sorted to isolate valuable elements.
The fine powdery substance resulting from the shredding and sieving processes is known as "black mass." It contains valuable metals like lithium, cobalt, nickel, and manganese. This black mass undergoes further processing through hydrometallurgical methods (involving leaching, solvent extraction, and precipitation) or pyrometallurgical methods (involving smelting and refining) to recover these metals.
More efficient recycling techniques often involve hybrid approaches combining both pyrometallurgy and hydrometallurgy. The recovered metals are then reused to produce electrode materials for the new batteries.
However, recycling of black mass can be challenging – partly because LIBs are not all the same. Specifically, there are two types of prominent chemistries – NMC (Nickel, Manganese, Cobalt) and LMFP (Lithium Manganese Iron Phosphate). Within NMC there are variants line NCM111, NMC622, NMC811 etc., where numeric indicates the relative atomic percentage of each element. Likewise, LMFP may have a variable amount of manganese. Variable chemistry necessitates that the black mass should be properly characterized and graded before being put into the recycling process.
The variable chemistry means there is often limited control over incoming types of batteries in lithium-ion battery recycling. Consequently, any treatment process for battery recycling must include an evaluation of the incoming batteries’ chemistry and crystalline phases. Our X-ray and neutron-based solutions can support you in this process – with both chemical composition and crystalline phase analysis.
Moreover, the efficiency of the hydrometallurgical leaching process can be evaluated using our online and lab-based XRF solutions including the analysis of incorporated impurities. Additionally, our particle size analyzers can be used to determine the particle size across the recycling process from black mass to finished products.
Chemical composition analysis of recycled li-ion battery materials
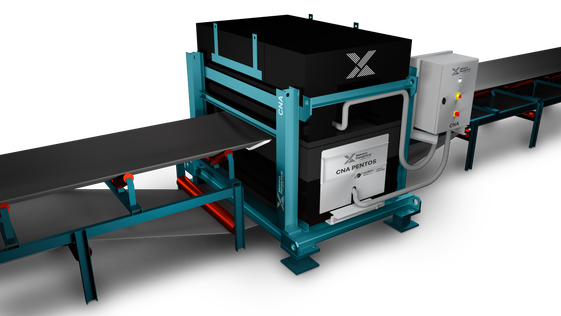
The elemental composition of the extracted black mass can be analyzed online with our CNA cross belt analyzer or offline using our range for XRF systems.
On-line Cross belt elemental analysis: The variable chemistry of recycled batteries means that the extracted black mass is a heterogeneous material, making lab analysis of a small sample non-representative of the bulk of the material. Cross-belt online analyzers can analyze the bulk black mass extracted at an industrial scale, providing an average composition of the entire material. Our CNA Pentos cross belt analyzer, based on the pulsed fast thermal neutron activation (PFTNA) switchable neutron technology, offers direct bulk measurement of all key elements like Ni, Co, Mn, Fe, P etc. in the incoming black mass.
CNA provides high-frequency online elemental analysis of the bulk material on the belt. No sampling is required as material is measured in real-time on the conveyor belt. Its compact and rugged design is completely underneath the belt - variation of belt load and particle size common in the extracted black mass doesn’t affect the performance of the system. This key design feature helps to provide stability and representativeness for efficient process control.
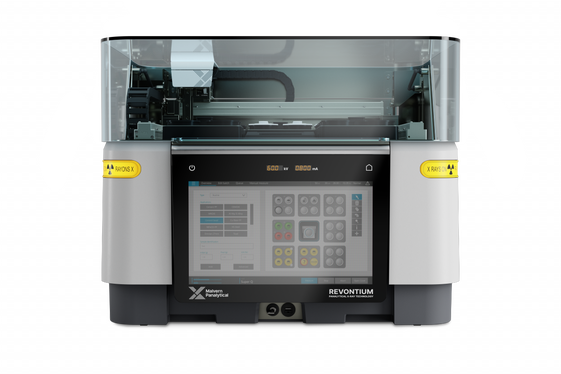
X-ray fluorescence (XRF) is another technique that can be used to analyze black mass in the lab or close to the process. X-ray fluorescence (XRF) significantly supports the battery recycling process by providing a rapid and accurate analysis of the elemental composition of used batteries with high precision. Its high precision enables recyclers to identify and quantify valuable materials such as lithium, cobalt, nickel, and manganese, optimizing the recovery process. It can also monitor the quality of recovered materials, ensuring they meet specifications for reuse. Additionally, XRF detects hazardous elements, facilitating safe handling and disposal.
For the major elements, XRF provides a simpler and more accurate way of measuring elemental composition than ICP, because it does not require any sample dilution or acid digestion.
Many leading battery companies use our benchtop Epsilon 4 EDXRF or Zetium WDXRF spectrometers to analyze their recycled materials. We have also introduced the Revontium range of high-performance EDXRF that can analyze elements and impurities in black mass with high accuracy and precision.
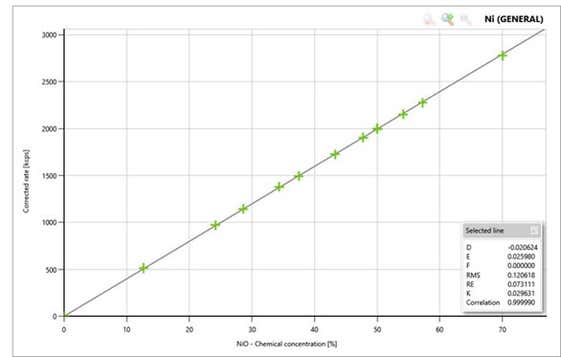
Accuracy of XRF analysis depends on the quality of calibration standards. Malvern Panalytical has developed its in-house certified calibration standards, which together with the Eagon 2 or FORJ sample fusion systems can provide a perfect recipe for accurate quantitative elemental analysis.
Figure 1 (right): A typical calibration line of Ni using our NCM reference standards measured on our Epsilon 4 XRF spectrometer.
Analysis of leached solutions
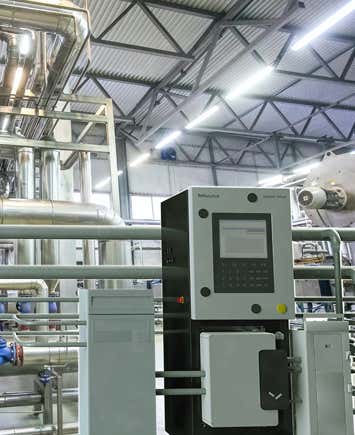
The elemental composition analysis of the leached solutions in hydrothermal extraction can provide valuable information about metal extraction efficiency. This can be analyzed in line with our Xflow range of XRF analyzers.
On-line liquid analysis with the Epsilon Xflow enables fast and accurate control of your process parameter.
Epsilon Xflow provides real-time data insights, enabling you to manage your production processes more efficiently and reduce your operational costs.
Crystalline phase analysis of black mass
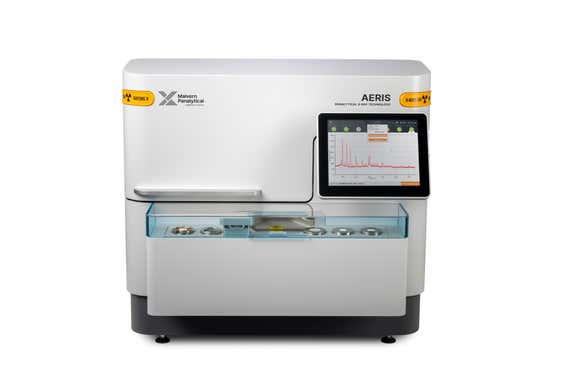
The battery recycling pre-treatment process may also be affected by the crystalline phase of the battery materials. And, when it comes to crystalline phase analysis, X-ray diffraction is the technique of choice. Our Aeris compact X-ray diffractometer – an easy-to-use instrument with superb data quality – can be used to accurately analyze crystalline phase composition in black mass and recycled battery materials.
Figure 2: Typical XRD analysis of black mass crystalline phases measured on our Aeris diffractometer.
Particle size and shape
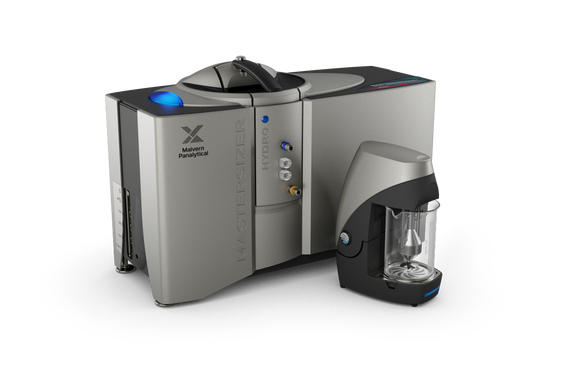
Particle size and shape play an important role across the entire value chain of battery recycling from black mass to finished output materials. Black mass needs to be ground to a certain particle size for efficient leaching of metals during hydrothermal extraction.
Many recycling companies produce battery precursor or electrode materials as their end-product, where particle size and shape are used as critical quality parameters.