To improve their cement's quality and consistency while supporting sustainability and reducing production costs, manufacturers need reliable material analysis solutions. Solutions like Malvern Panalytical's world-leading instruments. Whether it is X-ray diffraction (XRD) for mineralogical analysis, X-ray fluorescence (XRF) or Activated Neutrons Cross Belt Analyzers (CBA) for chemical analysis, or Laser Diffraction (LD) for particle size distributions, our cement portfolio provides a one-stop set of solutions for all parts of the production process. These solutions integrate seamlessly into your existing production and come with support you can count on, anywhere in the world.
As the push for a circular, Net-Zero industry drives the use of alternative fuels and clinker replacements, robust elemental and mineralogical analyses are increasingly essential to high-quality cement production. At the same time, particle size analysis remains critical for optimizing grinding efficiency and final cement properties. More than ever, cement manufacturers need tight control of every step in the production process to achieve maximum efficiency, cost-effectiveness, and quality.
Which instrument for which operation in the cement process? Find the answer in the illustration below.
Cement analysis methods
Cement analysis plays a crucial role in ensuring the quality and performance of cement throughout its production process, and in decarbonizing its manufacturing.
X-Ray Fluorescence (XRF)
XRF is used for elemental analysis of cement, raw materials, supplementary cementious materials (SCM) and alternative fuels. It identifies the chemical composition by measuring the characteristic X-ray emissions from the sample.
Depending on the accuracy of the measurement and the required time to get a result, different sample preparations can be considered:
- Sample Preparation
- Crushing/Powder: The material is crushed to reduce particle size and analyzed as powder Pressed pellets are often preferred to loose powders to ensure sample homogeneity, minimize particle size effects, and facilitate accurate elemental analysis
- Fusion: For the best accuracy, samples are dissolved into a molten glass forming a flux, resulting in a homogeneous glass disk. This eliminates particle size and matrix effects
- Application
- Raw Material Characterization: Assessing raw material composition (e.g., limestone, clay, gypsum) to get the right clinker
- SCMs Addition: add the right content of SCMs to the clinker to get the right cement, based on SCMs chemical composition
- Quality Control: Monitoring elemental composition during production
X-Ray Diffraction (XRD)
XRD identifies and quantifies crystalline phases in clinker and cement, as well as alternative fuels and SCMs (calcined clay).
Sample preparation is key to getting the right result and most of the time the biggest source of error. Two ways this can be used:
- Sample Preparation
- Grinding: Material is ground into a fine powder
- Pressing once ground: Pressed pellets are used for production control; this is the most reliable and recommended sample preparation method for most kinds of sample
- Application
- Phase Quantification: Determines the amount of each phase (e.g., clinker, gypsum) in cement
- Decarbonization: XRD empowers the cement industry to transition toward greener, more efficient processes by quantifying phases (clinker), exploring alternatives (Alternative fuels and raw materials) and driving innovation (new SCMs)
- Quality Assurance: Ensures consistent phase composition
Laser Diffraction
Know the range of particle sizes present in cement samples to enable better control of cement properties and operation costs. Particle size also plays a key role in reactivity and is therefore being used more often for other materials (clays, concrete fines etc).
Laser diffraction is based on the illumination of particles with a collimated laser beam. The scattered light is measured at various angles. Particle size information is derived from the diffraction pattern.
- Sample Preparation
- Grinding: In cement plants, dry analyses are carried out most of the time. This means the material is finely ground before measurement. In the case of real-time measurements, it is key to make sure analysis is carried out using a homogeneous and representative sample, which may require a larger volume and well-adapted sample collection
- Applications
- Compressive Strength target achievement: As particle size decreases, surface area increases. Finer particles enhance cement strength. 28-day strength can be affected by too many fine particles (< 2um), which causes cracking. Too many coarse particles adversely affect strength. This is why optimizing PSD between 2 - 32 microns is key
- Curing Properties: Laser diffraction aids in predicting and monitoring the curing behavior
- Blaine Number Enhancement: Beyond Blaine number, PSD reveals finer details and sensitivity to coarse fractions
Pulsed Fast Thermal Neutron Activation (PFTNA)
Process control technology used for real-time elemental analysis in cement production.
PFTNA allows continuous monitoring of elemental composition from quarry to kiln and can even be used to get perfectly controlled SCMs addition to the clinker for low carbon cements.
- Methods
- No Sample preparation is required, rocks on the belt are directly and fully analyzed (bulk analysis)
- Application
This technique is very useful for high-frequency analyses for use by artificial intelligence and machine learning models to optimize cement production with the right properties and lowest carbon footprint. It is commonly used at these key stages of cement production:
- Pre-blended Stock Pile to ensure raw materials' optimal homogeneity
- Raw Mix to get the right raw meal with lowest variations (LSF tight control)
- SCMs addition: Ensuring accurate additions to the clinker to get optimized reactivity and lower the clinker content (low-carbon cement)
In summary, these methods are essential at every stage of cement production:
- Raw Material Characterization: XRF, PFTNA and XRD analyze raw materials
- Quality Control: XRF, XRD, and Laser Diffraction to monitor production
- Final Product Quality: XRD and Laser Diffraction ensure proper phase composition
- Process Optimization: real-time analyzers are the eyes of the process – PFTNA and Laser Diffraction analysis guide adjustments. Automated XRD and XRF are of great support
All these techniques optimize cement production while also reducing the cost of manufacturing. Return on investment is short and cost of ownership low compared to the many benefits. Get in touch to learn more about how our instruments can help with improving your ROI.
Benefit from:
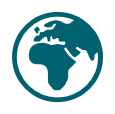
World-leading instruments
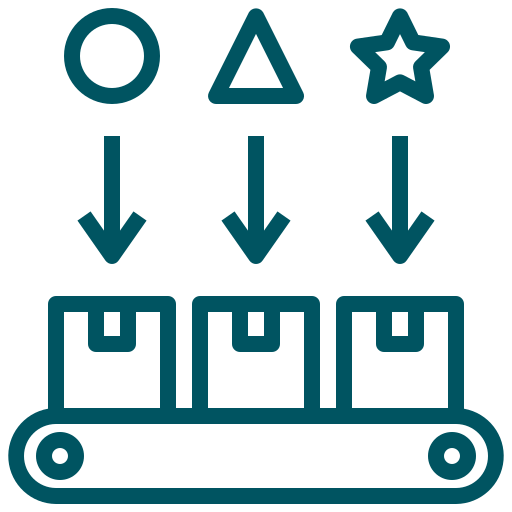
One-stop set of analytical solutions
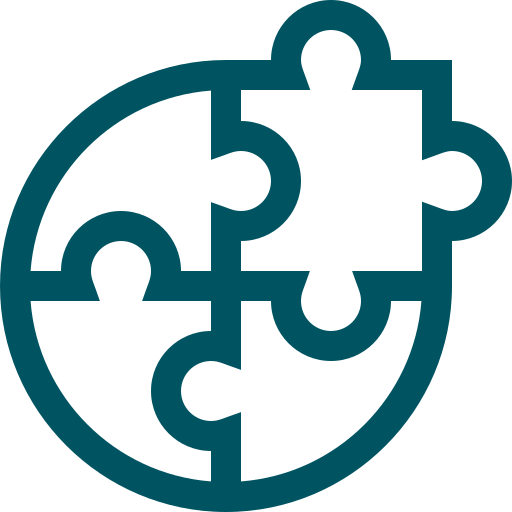
Seamless integration
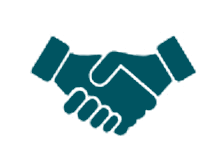
Global service and support
Sample preparation for raw materials extraction
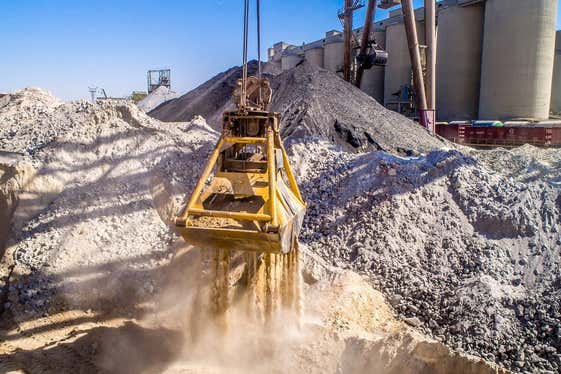
When selecting raw materials, manufacturers need to keep costs minimal, while ensuring that the materials are compatible with cement production. Especially when using alternative raw materials which introduce more variartions in the process, robust analyses help to monitor these changes to achieve the required specifications. Next to the costs of the materials also their impact on the process efficiency and the sustainability challenging targets (2050 Net Zero) must be considered. For this, chemical and mineralogical composition are crucial.
Our solutions help to minimize scrap and to optimize the mineralogical and chemical compositions of raw materials by providing high frequency analyses specifically when automated, and even more when used on- or at-line. They can do this both at the quarry and in raw mix proportioning. By providing results quickly, these instruments enable producers to reduce waste from sampling and ensure a stable kiln feed for energy efficiency in the remaining process (pre-homogenization and proportioning) and reduce CO2 emissions.
Our solutions
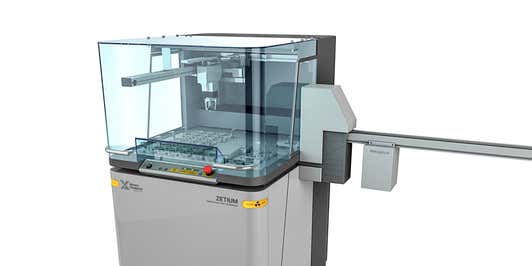
The Cement edition of Zetium
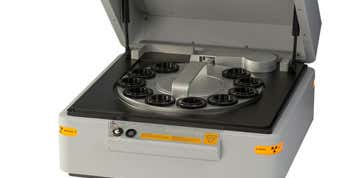
Epsilon 4
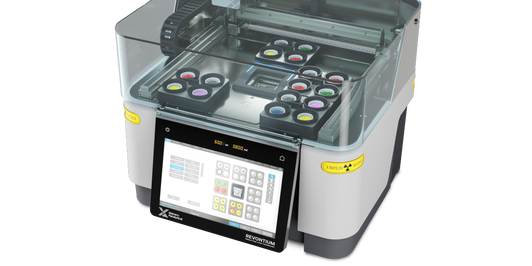
Revontium
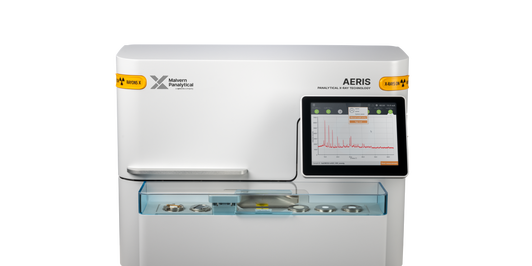
Aeris Cement edition
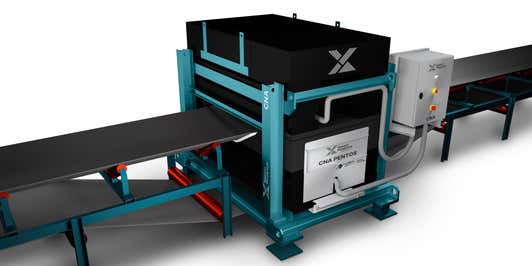
CNA Pentos
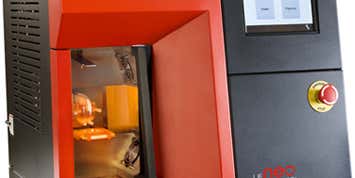
Claisse LeNeo
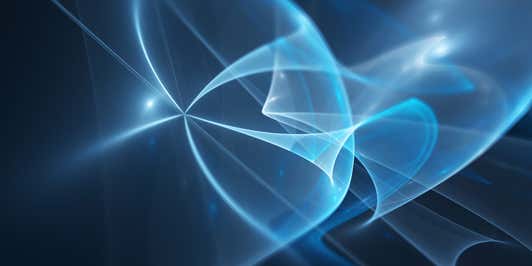
WROXI - Certified Reference Materials
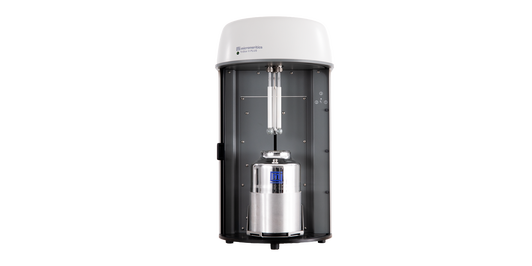
Micromeritics TriStar II Plus
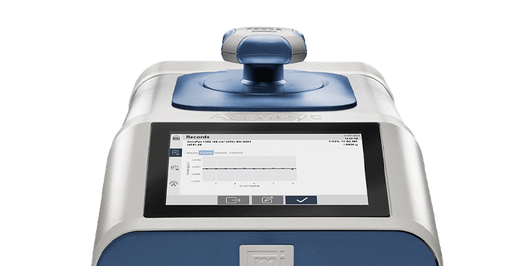
Micromeritics AccuPyc
Optimizing raw mix processing in the kiln
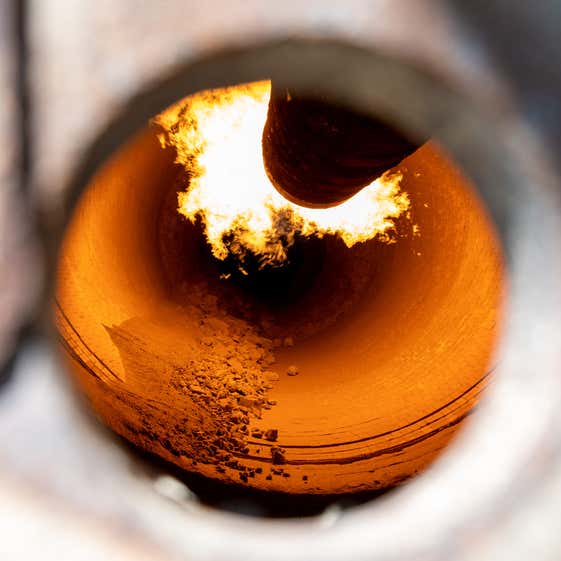
When it comes to raw mix processing, maximizing kiln efficiency is an essential part of reducing energy consumption, emissions, and maintenance requirements. Optimizing the materials that enter the kiln can help achieve this: the two main points of attention are monitoring the correct and stable mix chemistry and getting the proper raw grinding.
X-Ray Analysis Methods in Raw Mix Processing
Stable raw meal composition is also essential to ensuring consistent heat profiles in the kiln and delivering a high-quality end product with the right properties such as compressive strength and setting times. It also impacts energy consumption, grinding additive use, refractory life, additive consumption, fuel demand and other process factors. As an example, kiln oxidizing conditions are mandatory to avoid the decomposition of Alite C3S to Belite C2S and free lime. This stability can be achieved by controlling the chemical composition using XRF or on-line elemental analysis such as Neutron-Activated Cross-Belt analyzers, or by controlling mineralogy using XRD.
Optimal operating requirements are also to work with fine raw meal (avoid specifically coarse calcite and quartz grains): raw mix particles must be fine enough to ensure that they can mix and be ground well without hard burning. Then laser diffraction for particle size analysis can help ensure this.
Cement Raw Mix Particle Size
Optimal operating requirements are also needed to work with fine raw meal (avoiding specifically coarse calcite and quartz grains). Raw mix particles must be fine enough to ensure that they can mix and be ground well without hard burning. Then laser diffraction for particle size analysis can help ensure this.
The Mastersizer will be located in the lab and used for quality control, while the Insitec or the Labsizer will be used for process control.
Our solutions
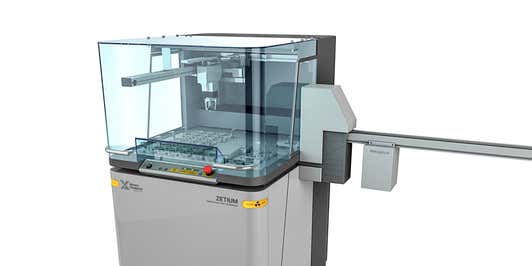
The Cement edition of Zetium
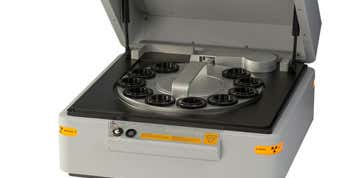
Epsilon 4
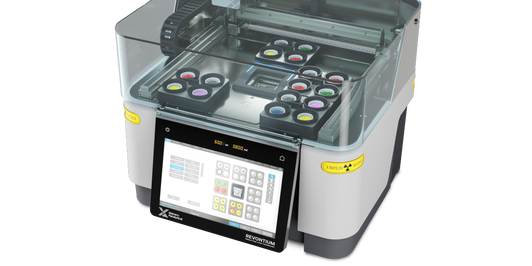
Revontium
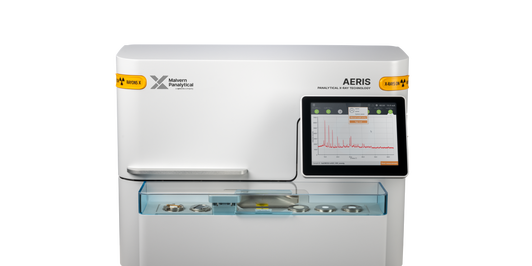
Aeris Cement edition
Mastersizer range
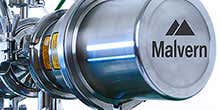
Insitec range
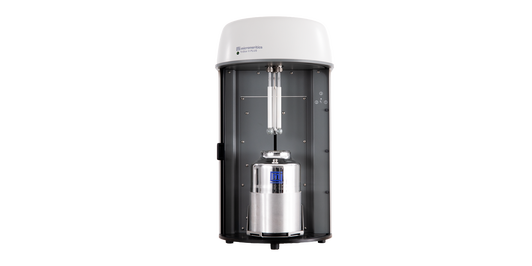
Micromeritics TriStar II Plus
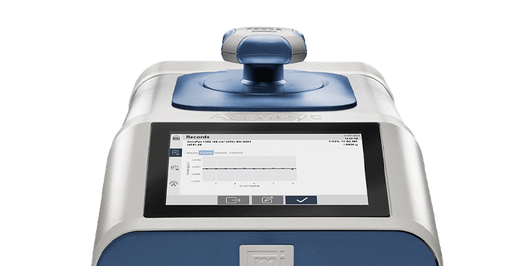
Micromeritics AccuPyc
XRF certified reference materials for cement analysis
WROXI is a synthetic, high-quality Certified Reference Materials (CRM) kit that covers a wide range of oxide materials such as ores, rocks, and geological materials. It has a dual purpose: either for primary fusion glass disk calibration, or to develop secondary pressed powder calibrations.
The beads-based WROXI-CRM base software package consists of 15 Certified Reference Materials, application templates and monitoring samples. Once completed with the WROXI-CRM Cement extension (9 additional CRMs), it becomes an off-the-shelf solution for primary and secondary element analysis in various raw materials, raw meal, clinker and cement samples.
Elemental analysis of alternative fuels used in cement production
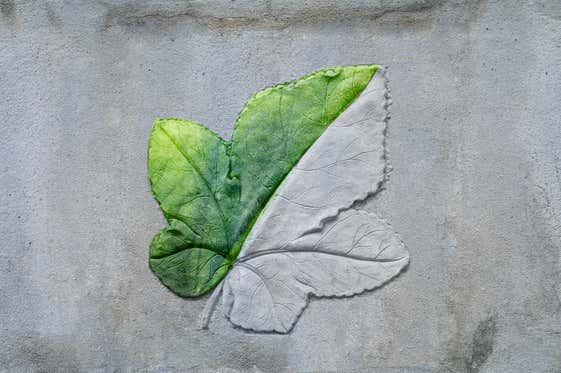
Increasingly, alternative fuels in the form of biomass, mixed fuels, or fossil waste with lower emissions factors are replacing resource intensive fossil fuels. By recovering the calorific value of fuel waste, these additive fuels help to reduce emissions from cement production.
But alternative fuels must be fully characterized for their safety, chemical, thermal, and physical properties to assess their effect on parameters such as flame temperature and heat exchange.
Our XRF elemental analyzers (Epsilon 4, Revontium and Zetium), cross-belt elemental analyzer (CNA Pentos-Cement), mineralogical compact X-Ray diffractometer (Aeris Cement) and automatic fusion sample machines (LeNeo, Eagon2 and FORJ) make this easier.
Our solutions
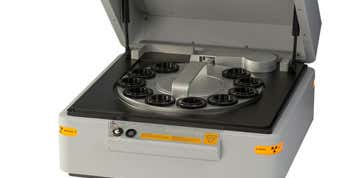
Epsilon 4
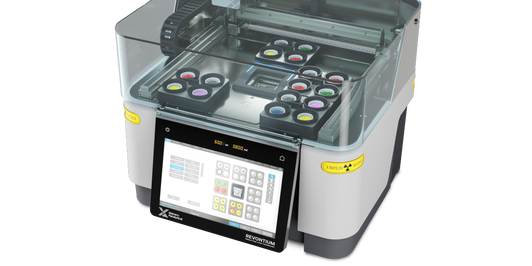
Revontium
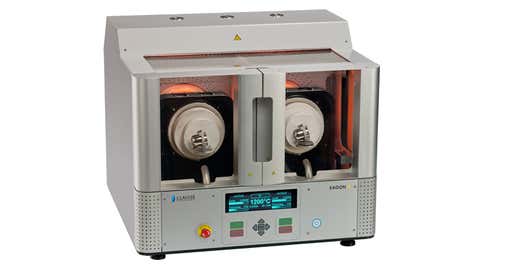
Claisse Eagon 2
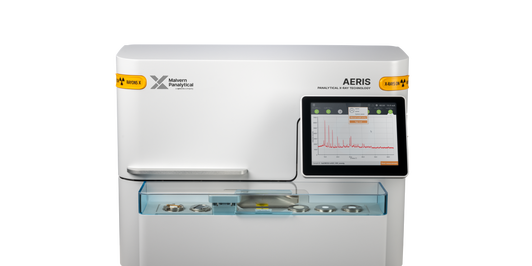
Aeris Cement edition
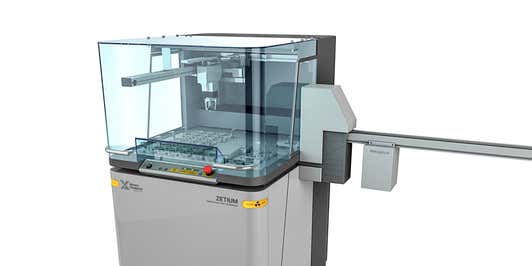
The Cement edition of Zetium
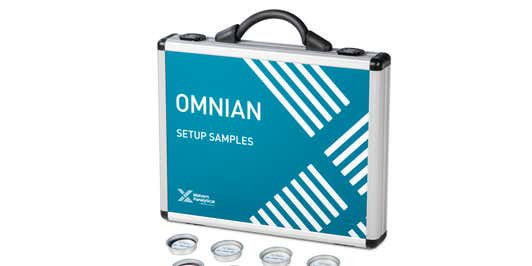
Omnian
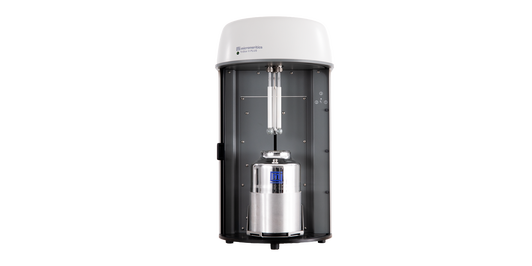
Micromeritics TriStar II Plus
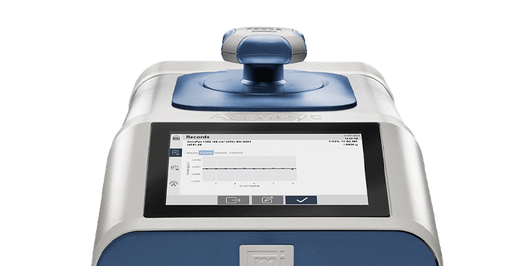
Micromeritics AccuPyc
Clinker production analysis methods
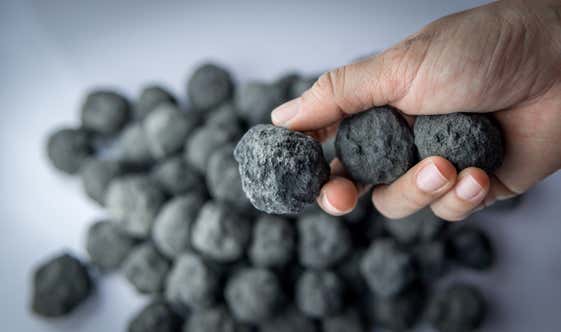
Clinker production results from pyroprocessing: raw meal preheating, calcination clinkerization, clinker cooling, and crushing. To achieve the right cement properties, as seen above, the proper calcination conditions have to be controlled, followed by a rapid quench of the clinker.
Attention is then on controlling the proper calcination (free lime), avoiding unwanted elements and maximizing positive mineral phases for the targeted properties of the cement.
XRD analysis of clinker mineralogy
To ensure proper calcination and the right clinker mineralogy, X-Ray diffraction is the best analytical technique: it allows the quantification of C3S content and type that influences strength development, C3A content and type that impacts fresh properties, and amount of free lime and periclase that should not be higher than targeted limits. Malvern Panalytical’s analytical solutions support this monitoring using the Aeris XRD compact diffractometer.
How XRF is used in clinker production?
In clinker production, XRF serves several crucial purposes:
- Raw Material Proportions Adjustment : XRF helps optimize the blend of raw materials (such as limestone and clay) for the raw meal to ensure the right mix for clinker production.
- Process Control : During clinker formation in the kiln, XRF monitors the process conditions to ensure consistent quality by frequently assessing elemental content. On top of classical elements (calcium, aluminum, iron, and silicon), unwanted elements (MgO, Alkali, sulfur, Chlorine) are controlled in internal recycle streams from fuels or raw mix.
- Clinker Quality Assurance : XRF quantifies major, minor and some trace elements in the clinker directly correlated to cement performance characteristics.
- Phase Composition Insights : XRF helps to identify the chemical composition of clinker phases (e.g., C3S, C2S, C3A, C4AF) to guide process adjustments and final cement properties.
In summary, XRF (Epsilon 4, Revontium, Zetium) enhances clinker quality, process efficiency, and overall cement production.
Sustainable approach to clinker production
Finally, as seen above, in a sustainable approach, manufacturers target not only the high quality of clinker but also want to save energy and resources, and reduce emissions.
Pyro processing of clinker needs calcination at 1450 °C and related energy is usually satisfied by firing coal at calciner and kiln main burner. To save energy and decrease CO2 emissions, waste and biomass are used as alternative fuels more and more. Alternative raw materials are also used.
Dosages of such Alternative Fuels or Alternative Raw Materials require some specific controls to avoid negative effects on the clinker reactivity. Our X-Ray solutions enable you to enjoy the benefits of alternative solutions for clinker production without worries about the impact on quality.
Our solutions
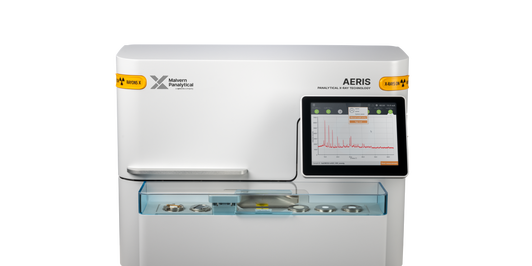
Aeris Cement edition
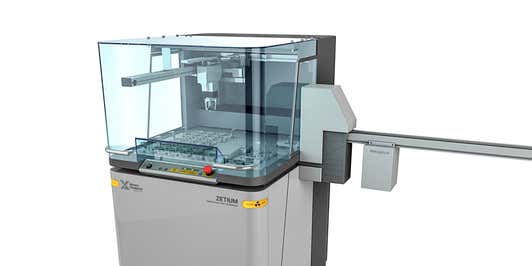
The Cement edition of Zetium
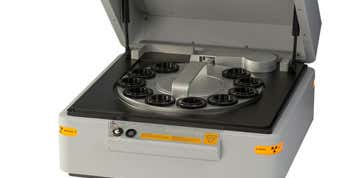
Epsilon 4
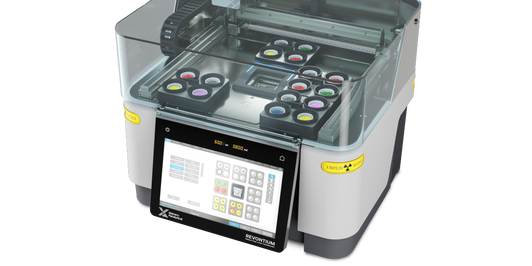
Revontium
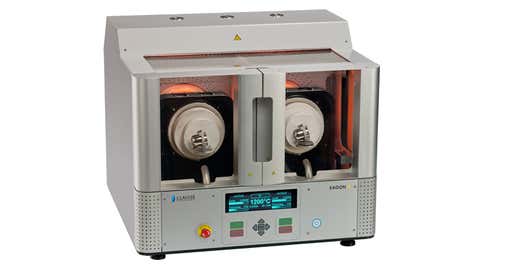
Claisse Eagon 2
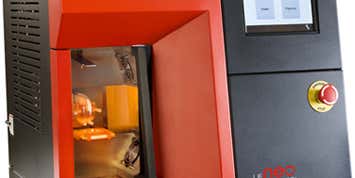
Claisse LeNeo
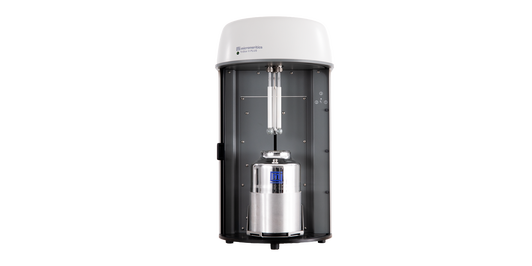
Micromeritics TriStar II Plus
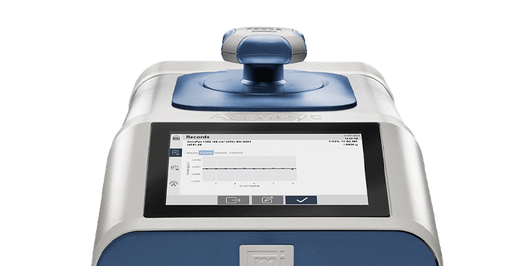
Micromeritics AccuPyc
Sustainable cement analysis methods
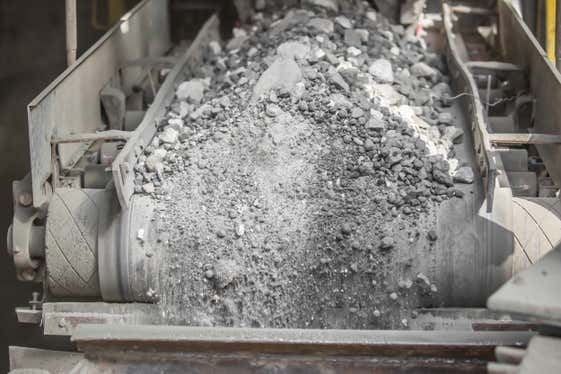
Cement is produced by grinding clinker with different active ingredients (SCMs) into a fine powder to achieve the desired properties of cement. The most common additions are gypsum and mixed materials such as fly ash, blast-furnace slag, limestone, natural pozzolans and calcinated clays. They are ground to the required fineness and mixed in the right proportions to produce targeted crystalline cement phases.
To reduce energy consumption, over-grinding must be minimized. The granularity of the finished cement affects its rate of hydration reaction, as well as the amount of water, retardant, and dispersant needed, and is a key factor in determining the strength of the cement. Our particle sizing solutions can help to achieve optimum cement granularity. Thanks to their fast, real-time analysis including in the challenging process environment, they allow producers to react quickly to any anomalies and monitor ambitious accurate targets. In this way, they help enable significant energy savings and optimal short-term and long-term cement strengths. What’s more, they can be quickly and easily installed for minimal disruption.
Monitoring of Sulphate content and mineralogical composition type (linked to dehydration during grinding) is crucial for achieving the right fresh and hardened cement properties. Regarding blended cement, closely controlling composition (including amorphous materials) is required to meet clients’ specifications and CO2 emissions targets. Our X-Ray fluorescence and X-Ray diffraction instruments are of great help for this.
Our solutions
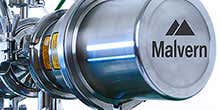
Insitec range
Mastersizer range
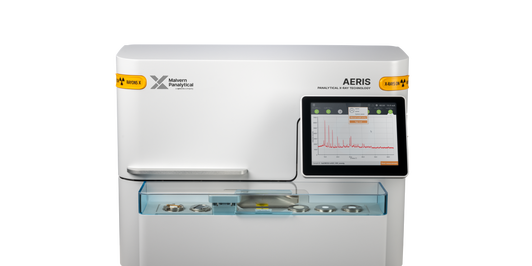
Aeris Cement edition
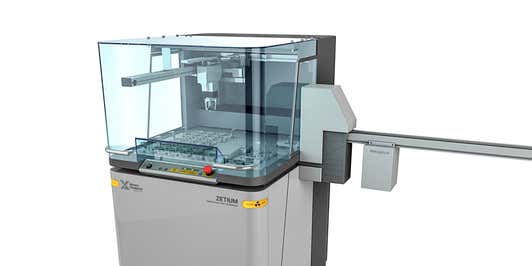
The Cement edition of Zetium
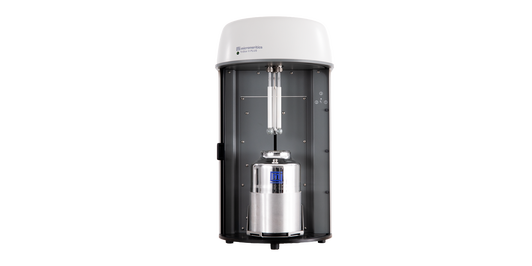
Micromeritics TriStar II Plus
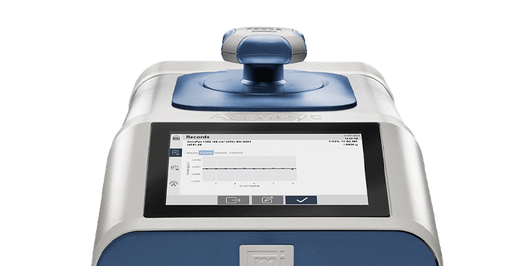
Micromeritics AccuPyc
Concrete: confirm the shipment quality – ready for recycling
Concrete is made up of three basic components: water, aggregate (rock, sand, or gravel) and cement. Cement, usually in powder form, acts as a binding agent when mixed with water and aggregates. This combination, or concrete mix, will be poured and will harden into the durable material with which we are all familiar.
Concrete recycling is becoming an increasingly popular way to utilize aggregate left behind when structures or roadways are demolished. In the past, this rubble was disposed of in landfills, but with more attention being paid to environmental concerns, concrete recycling allows reuse of the rubble while also keeping construction costs down.
In both cases, the main attention is that the concrete meets the promised workability, qualities once hardened (resistance to freezing, water tightness, wear resistance, strength), and the price of use (water quantity).
Composition and material sizes are again of great importance. Our laser or X-Ray based instruments provide the required information for a high-quality check of such characteristics.
Our solutions
Mastersizer range
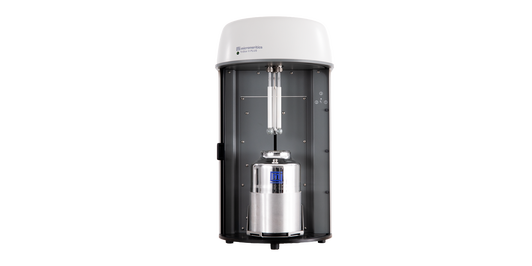
Micromeritics TriStar II Plus
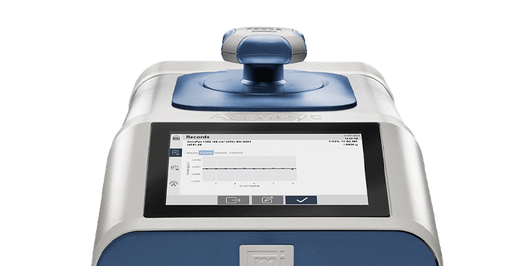