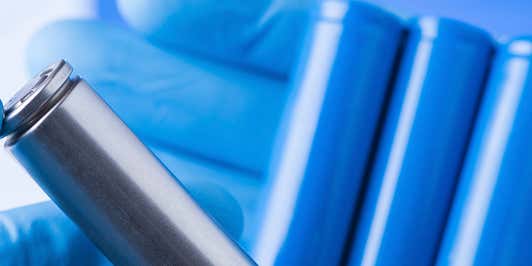
Energy storage materials play a crucial role in the transition to sustainable energy solutions, with batteries and green hydrogen taking the lead in transforming mobility, grid energy and industrial sectors.
Batteries, particularly lithium-ion batteries, are widely used due to their high energy density, long cycle life, and efficiency, making them essential for portable electronics, electric vehicles, and grid storage.
On the other hand, green hydrogen, produced through the electrolysis of water using renewable energy sources like wind and solar, offers a clean and versatile energy carrier. It can be stored and transported for use in various applications, including transportation, industrial processes, and power generation.
The integration of advanced battery technologies and green hydrogen systems is pivotal for reducing greenhouse gas emissions and transitioning to a sustainable energy future.
Battery materials characterization solutions
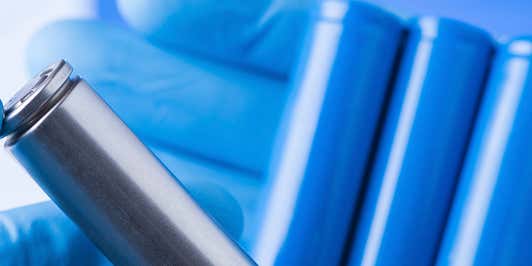
Analytical solutions play a vital role in the production of battery materials and hydrogen catalysts by providing precise insights and optimizing processes.
For battery materials, analytical techniques such as Laser diffraction, optical imaging, X-ray diffraction (XRD), and X-Ray Fluorescence (XRF) help in understanding the particle size, particle morphology, crystal structure, and elemental composition. This knowledge aids in improving the synthesis methods, enhancing material properties, and ensuring consistency and quality.
Additionally, in-operando XRD helps in evaluating the performance of battery materials under real operating conditions, guiding the development of higher-capacity and longer-lasting batteries.
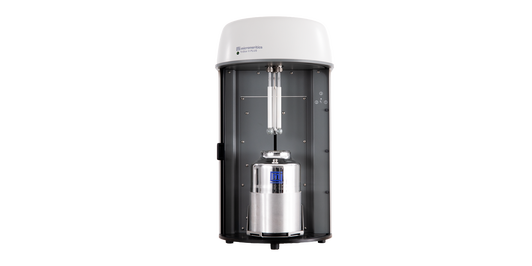
Micromeritics TriStar II Plus
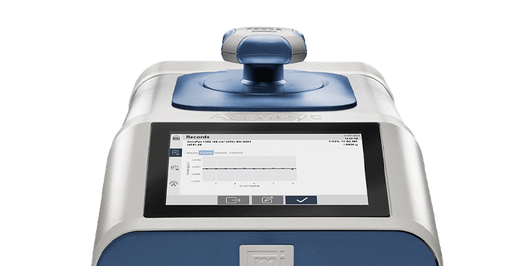
Micromeritics AccuPyc
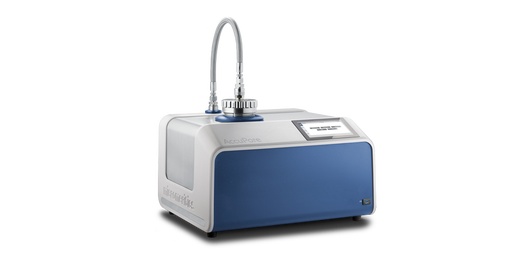
Micromeritics AccuPore
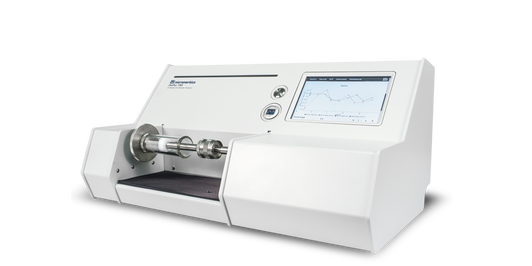
Micromeritics GeoPyc
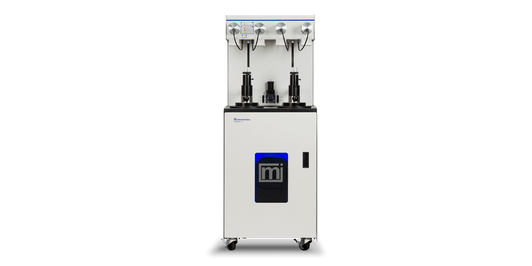
Micromeritics AutoPore V
Hydrogen catalyst analysis
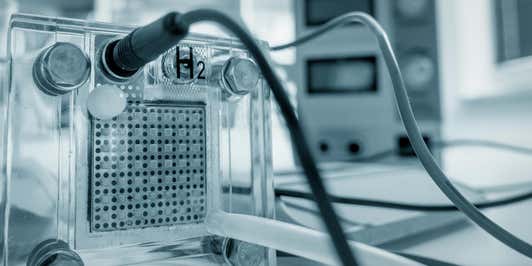
Analysis of Catalytic Ink for Proton Exchange Membrane Fuel Cells (PEMFC’s)
For hydrogen catalysts, laser diffraction and dynamic light scattering can be used to investigate components of catalysts and inks from nano to micro scale.
XRD can help to investigate catalyst stability and agglomeration, which can deteriorate its performance. XRF can be used to analyze impurities in the catalysts, which may degrade its catalytic activity.
These insights are crucial for designing more efficient and stable catalysts. By leveraging these analytical tools, researchers can identify optimal compositions, understand degradation mechanisms, and develop catalysts that improve the efficiency and cost-effectiveness of green hydrogen production.
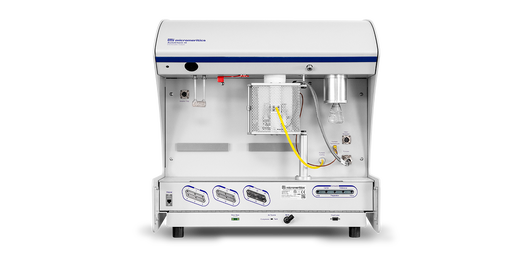
Micromeritics AutoChem III
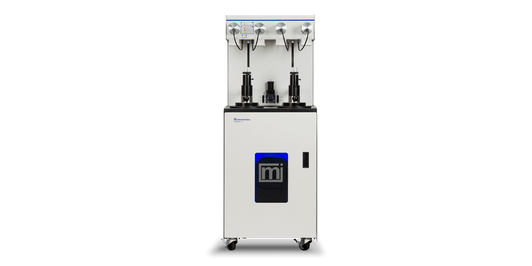
Micromeritics AutoPore V
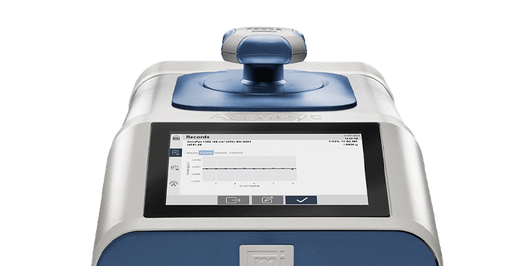
Micromeritics AccuPyc
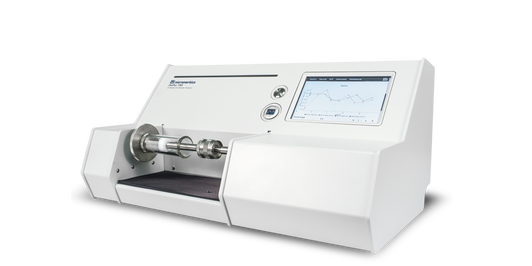
Micromeritics GeoPyc
Further reading
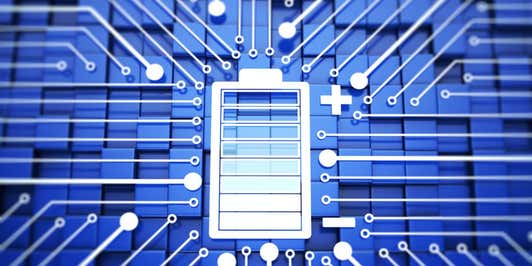
What XRD configuration shall one use to analyze battery cathode materials?
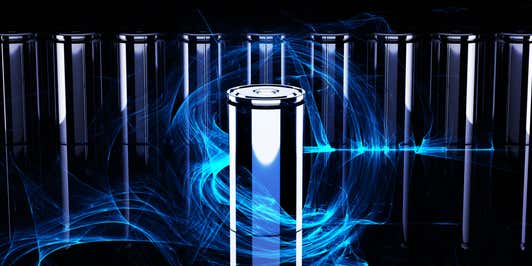
Elemental composition analysis of Nickel-Manganese-Cobalt cathodes and their precursor materials using Epsilon 4 ED-XRF spectrometer
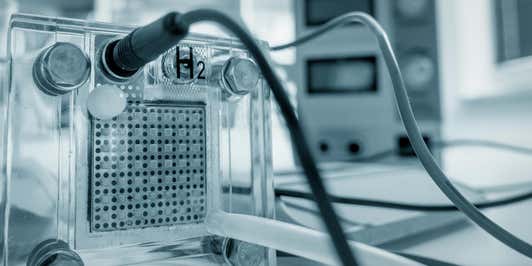
Analysis of Catalytic Ink for Proton Exchange Membrane Fuel Cells (PEMFC’s)
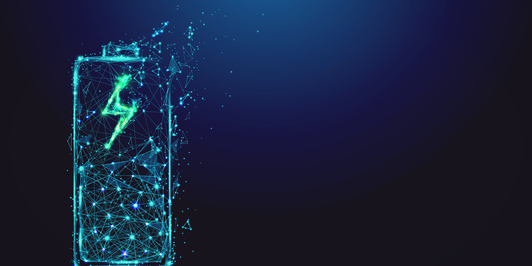
Battery manufacturing: Reliable, adaptable particle sizing using the Mastersizer 3000+
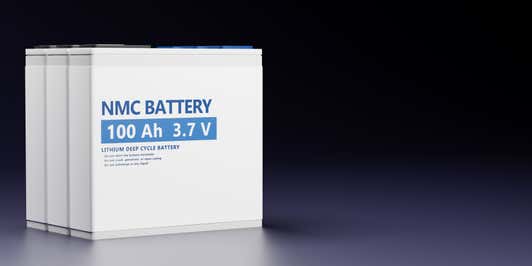
Elemental composition analysis of Nickel-Manganese-Cobalt cathodes and their precursor materials using Zetium WDXRF
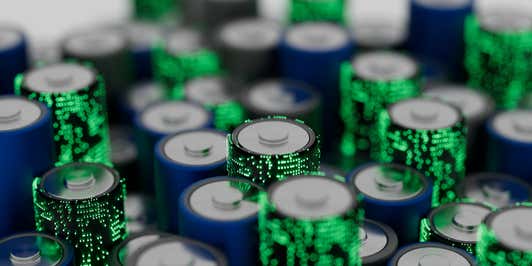
Bulk analysis of battery black mass by CNA
University of Pittsburgh: delivering sustainable solutions to current challenges in energy storage and conversion
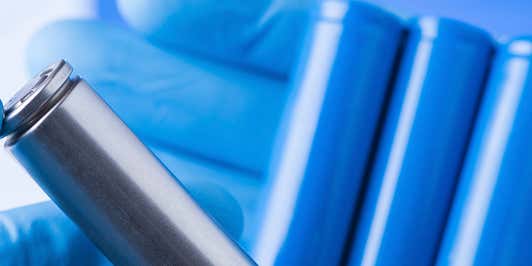
Analytical toolkit for the optimization of battery electrode materials
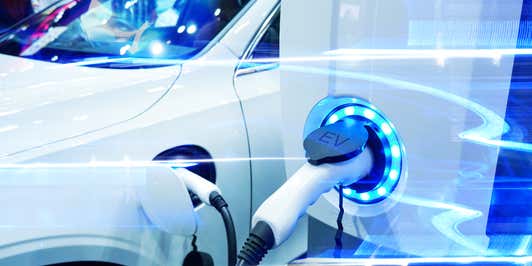